This past week has seen whirlwind of activity from a lot of people to make the first Rebounds out of the production molds a reality.

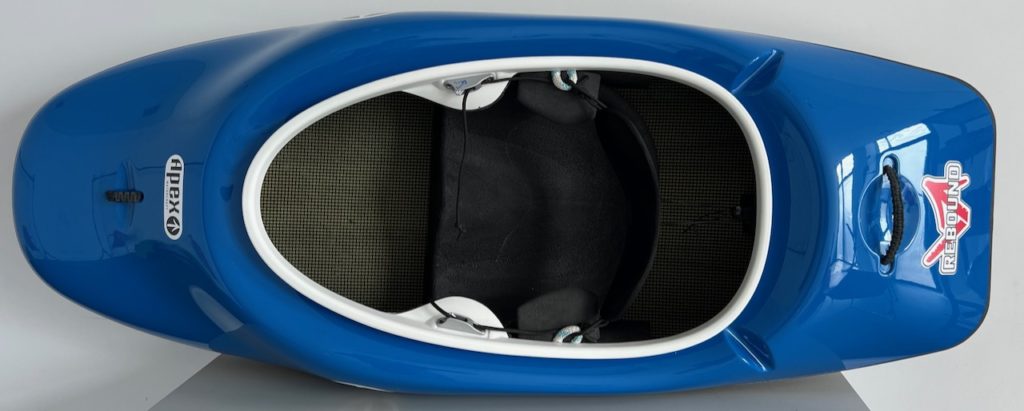
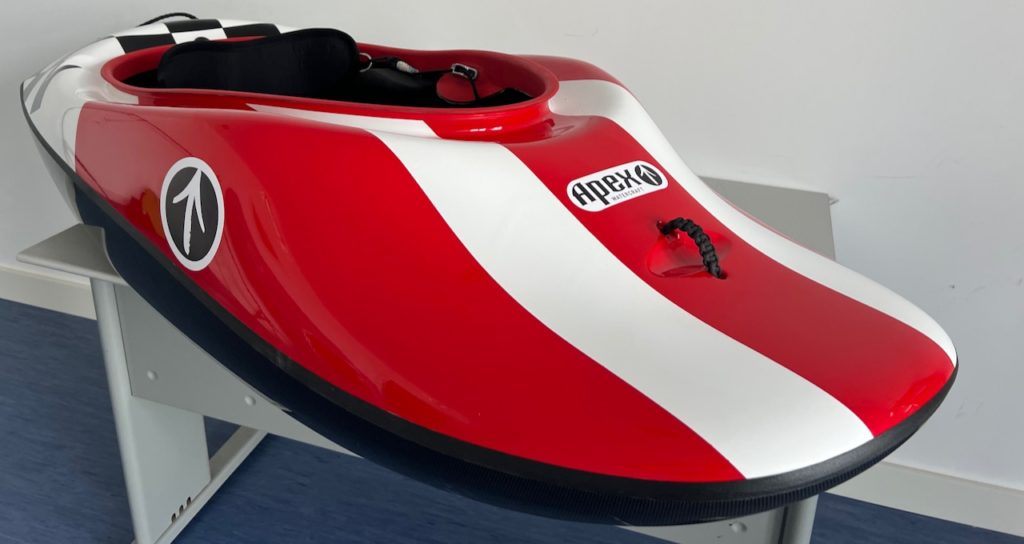
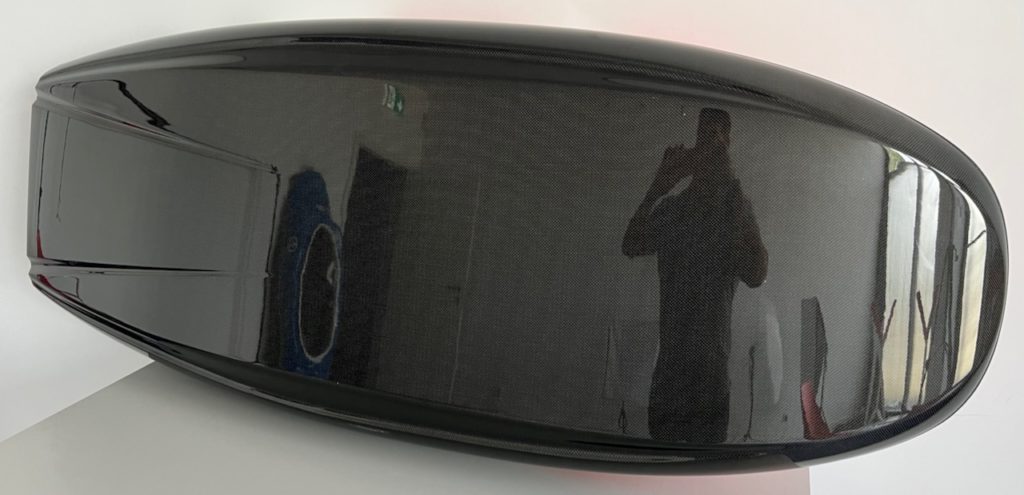
There is a lot that goes into a new design, at a new factory with new people. The process is far from perfect at this stage and I have a lot of work to do before we hit our stride. However, the talent, tools, and energy needed to make it happen are all coming together into an orchestrated effort and that effort is showing the results.
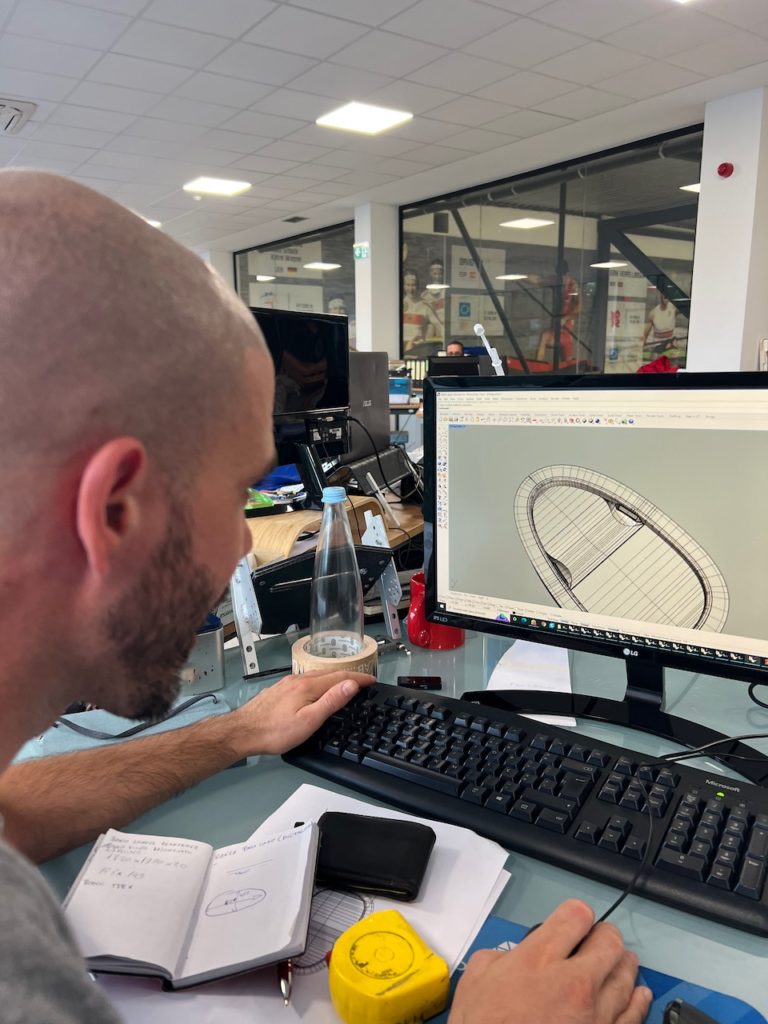
The first two boats, one for me and one for Tomasz Czaplicki were molded, and all of the outfitting made, and assembled this past week.
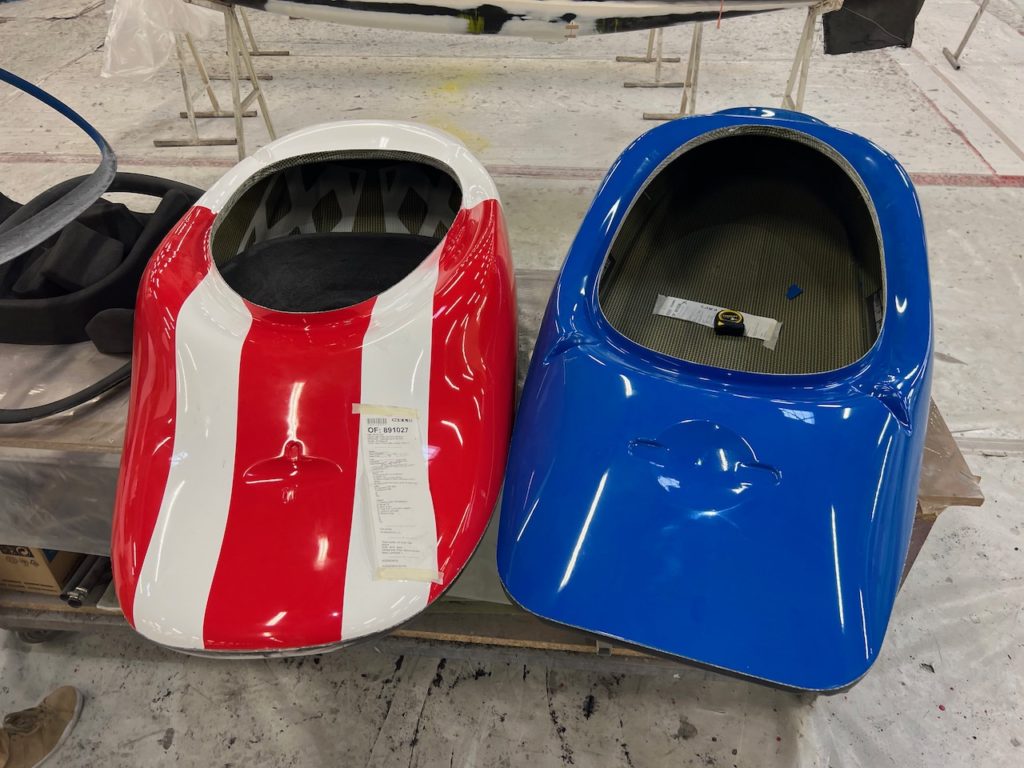
We had some real challenges, such as the wrong file was used to cut a cockpit rim mold, so we had to go into overtime to cut a new mold, make new rims, and get them on the boats in short order. That experience spoke volumes for Nelo, himself. The owner of Nelo. He jumped in the project with boat feet and prioritized the cockpit rims- staying until 9pm the night the CNC machine finished cutting and finished and sprayed the molds so we could lay up the first rim in the morning. He was then there at 6am to get a team on the making of the rims as we needed two rims molded, trimmed, and installed on the kayaks in one day. Anyone who has ever worked with composites, knows that it is “impossible”. However, it happened. Molded, put in a hot oven, popped a bit early, trimmed, and the second one sprayed right away with Gel coat and repeated.

Areas that need improvement still:
There was a few other issues in the process, such as the wrong hull lay-up used on both of our boats that, while it will work fine, it is both heavier and not as stiff. We will change that lay-up back to the one used in my prototype, plus some additional improvements that was specified, but fell through the cracks. Again, a growing pain that is best dealt with right away. How heavy? 1.5 pounds more than the prescribed weight and more hull flex- when you stand on it you can see some flex, versus almost no flex at all. These boats have vertical foam walls in them to overcome that.

Other challenges to overcome/changes to be made- (I am listing all of the things that still need work, so you don’t think everything is done already and we are moving on…. In manufacturing, there is no such thing as everything is perfect. You spend all day everyday figuring out how to improve each step and process. The CNC Machined seat is awesome. The gluing of the foam blocks together before machining the seat is not the best glue. That is being changed.

Thigh braces- The way the “Throat” of the cockpit area on the deck is trimmed determines how high or low the cockpit rim is when installed. The thigh braces are attached to the rim so the height is critical. Having very engaged “Thigh Hooks” in a freestyle kayak is something of a catch 22. If you are smaller in leg size (not a fat leg), you can afford more hook, but if you have big legs, the hook gets in the way. Right now the thigh hook is pretty aggressive at the height it is installed. I think I will need to raise it up a tad with a slightly higher trim point on the deck area at the cockpit rim. I am super secure and tight and it is perfect for me, so no complaints on my end. 🙂
Grab handles are about 1/2” too long on the stern, I will tighten that up.
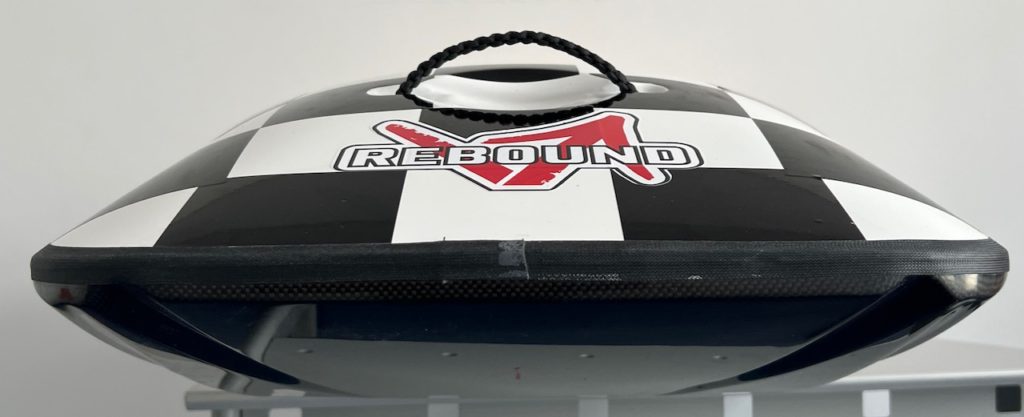
OK… that is all of the “negatives” I can find at the moment. Now the positives:
The lamination of these boats is done with precision and skill in the perfect environment. The right materials, temperature, resin, mold preparation, timing between Gel coat and laminating, the best vacuum pump system, bagging materials, etc.. The top and bottom of the Rebound are molded at one time as a one piece kayak. They are not joined later. I added both inside and outside seams to these boats only because I wasn’t confident in the amount of layers joining the them together. Nelo has a good solution which is to add the inside “seam” tape during the one piece process for the next boats.

Assembly- I had Henrique overseeing the team putting the rim on my boat, adding grab handles, the rope that holds the backband, etc.. He is unreal in skill and knowledge and wants me to oversee the next batch of boats as well as in the end, it will take some more training before they know it inside and out. The forces on a whitewater kayak are unique to whitewater, and freestyle has its own challenges in extreme forces that no manufacturer who isn’t a freestyle kayaker could predict. I have had to dictate everything related to structure as everyone thinks I am way “overbuilding” the boat. I show videos that illustrate how the boat will be used and it helps them understand.

Boat bags- The boat bags are coming along nicely as well. Simple and not for extreme use, just to protect the boat and make it easier to transport without them getting abrasion. Also, perfect for flying with boats for anyone doing that. I have a couple of small changes for Gomes to implement, but he and his team are awesome and making anything that requires a sewing machine.
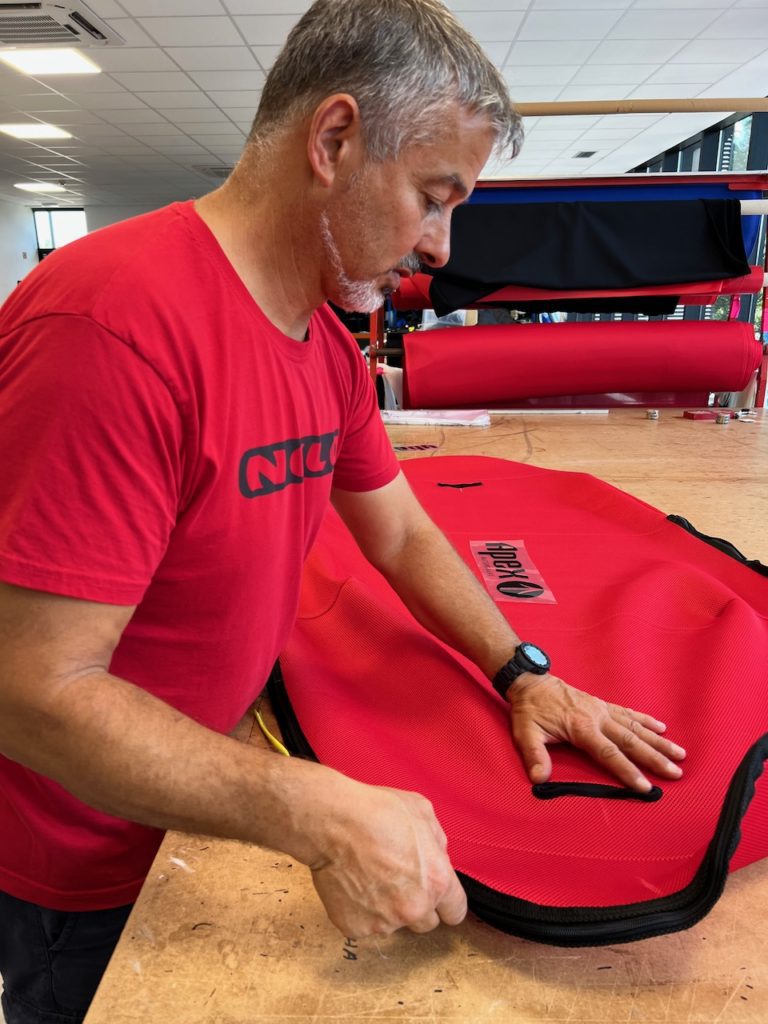
What is next? I am letting dealers and customers order boats now. The ordering system is just getting organized for the European dealers, and for USA/Canada customers, We have a few dealers already organized, and I’ll open up more this fall. Email me directly to get things started, however. eric@apexwatercraft.com It now looks like I am scheduling a container this week that will have the Tyr Fishing kayak, and Rebound medium, and Ringer medium in composite in it, and maybe the small Rebound. We’ll start molding those boats next week after we make the adjustments above, and it will take a while to make enough boats to fill that box. If you think you want a boat on that container- now is the time to let me know!

I am heading to Columbus to paddle my new boat and train for World Cup tomorrow. Tomasz Czaplicki is also waiting for his boat and I am sure he is wondering when that will happen. Tomorrow Tomasz!
Thanks again for the hard work on my behalf and on behalf of the Apex Watercraft current and future customers Team Nelo! Andre, Nelo, Sergio, David, Henrique, Gomes, Jone, and many more! Here are some more photos from this trip and those working on the boats.
Here is a video and some photos of the action:
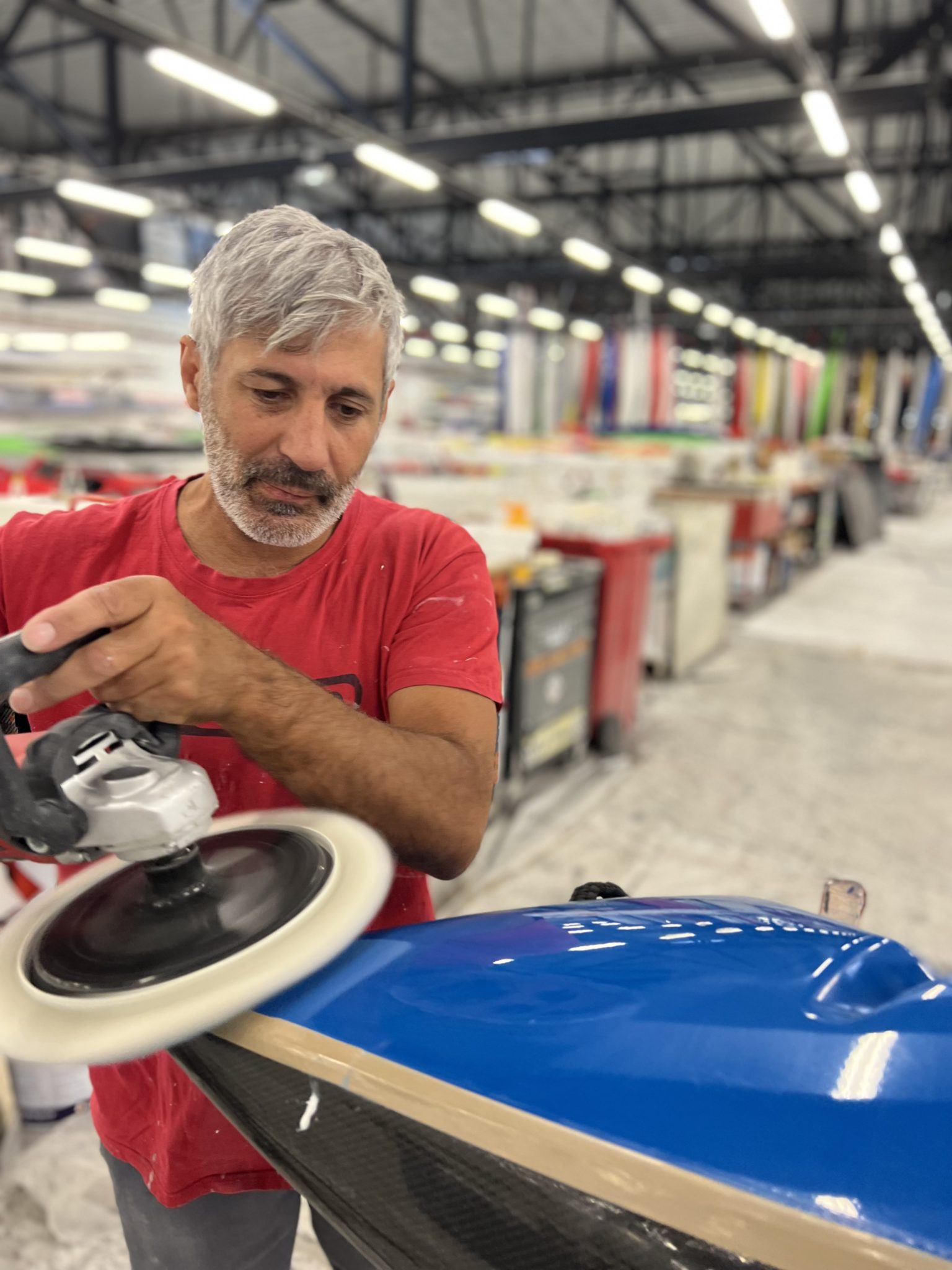
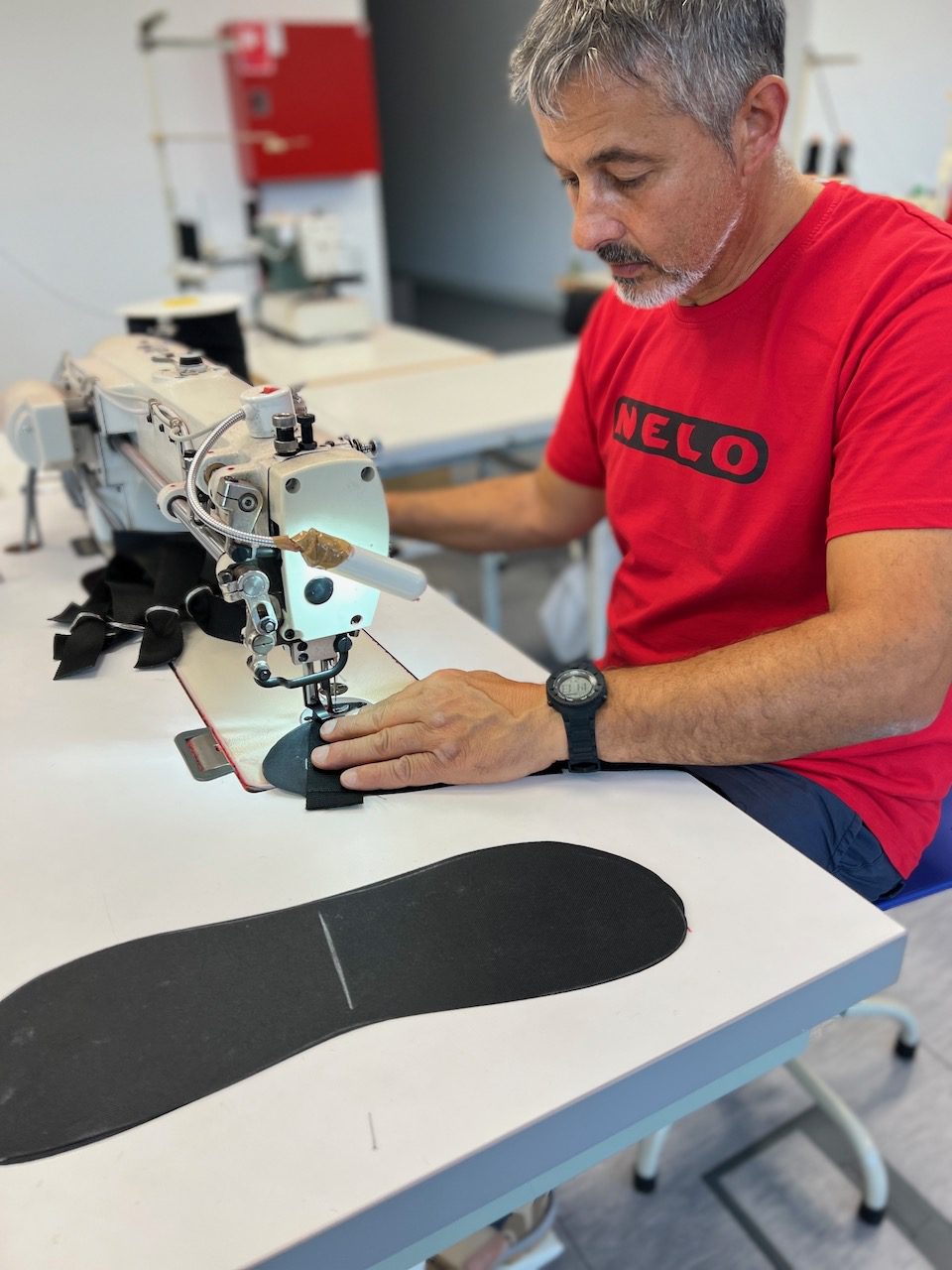
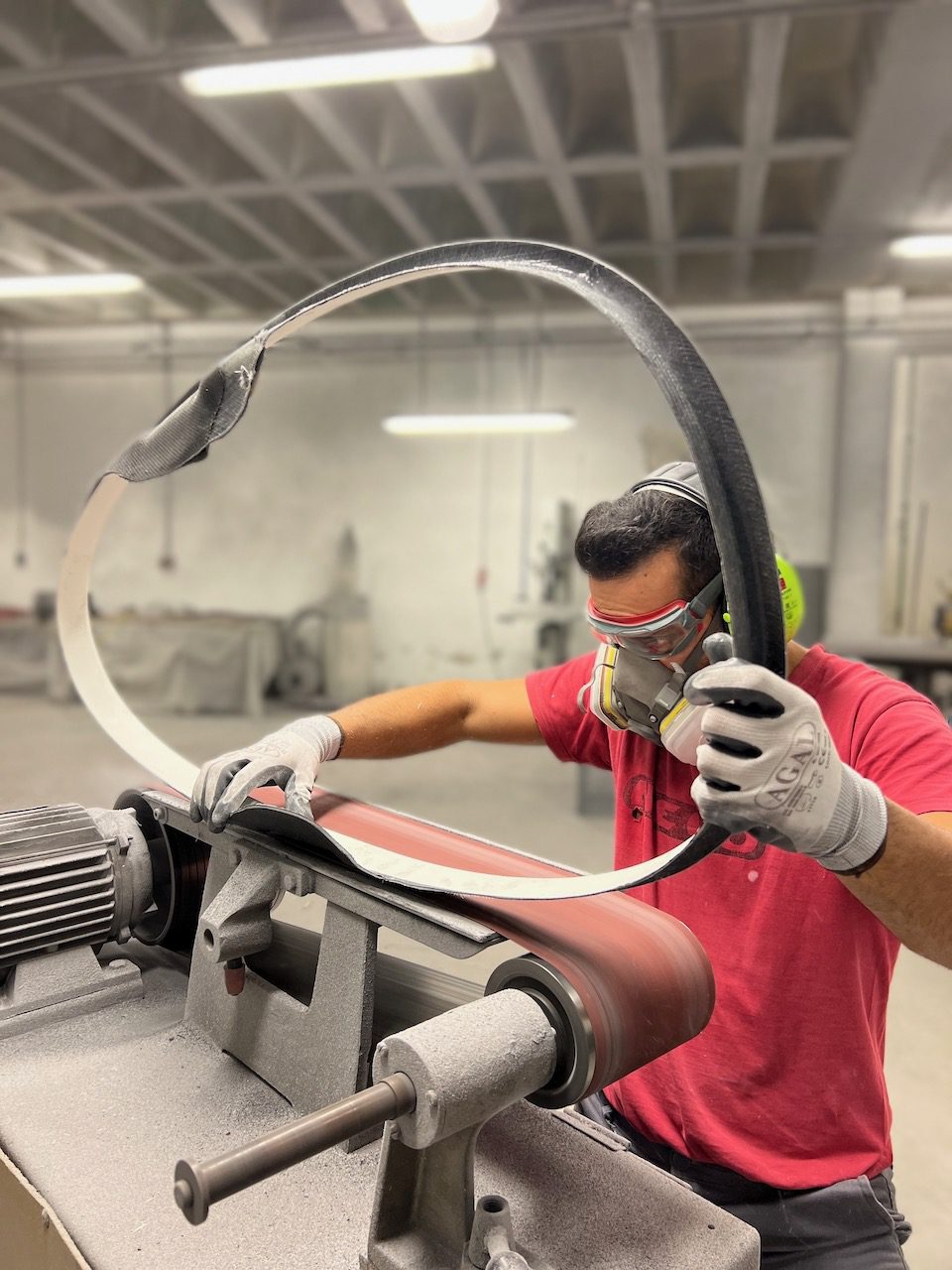
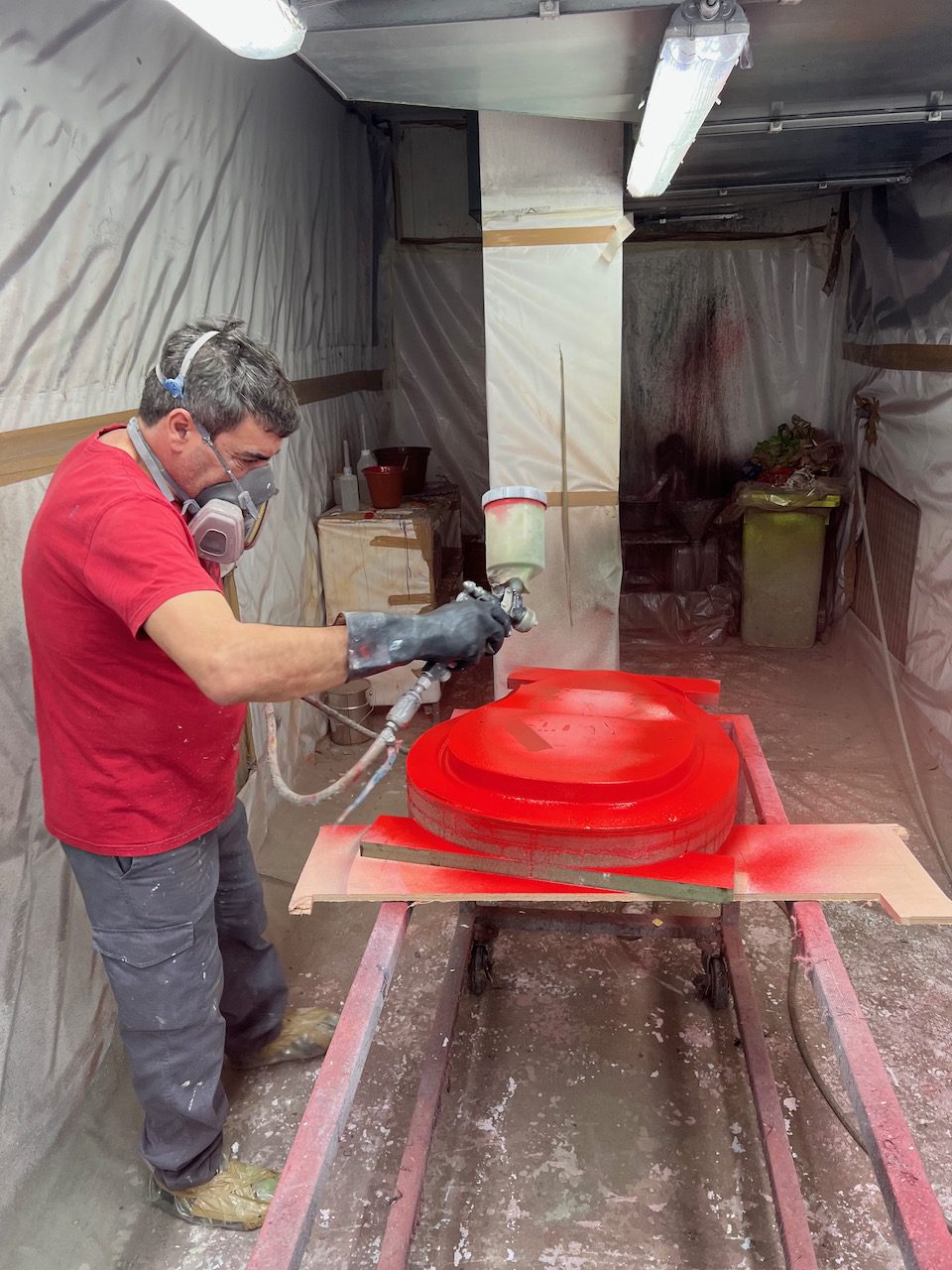

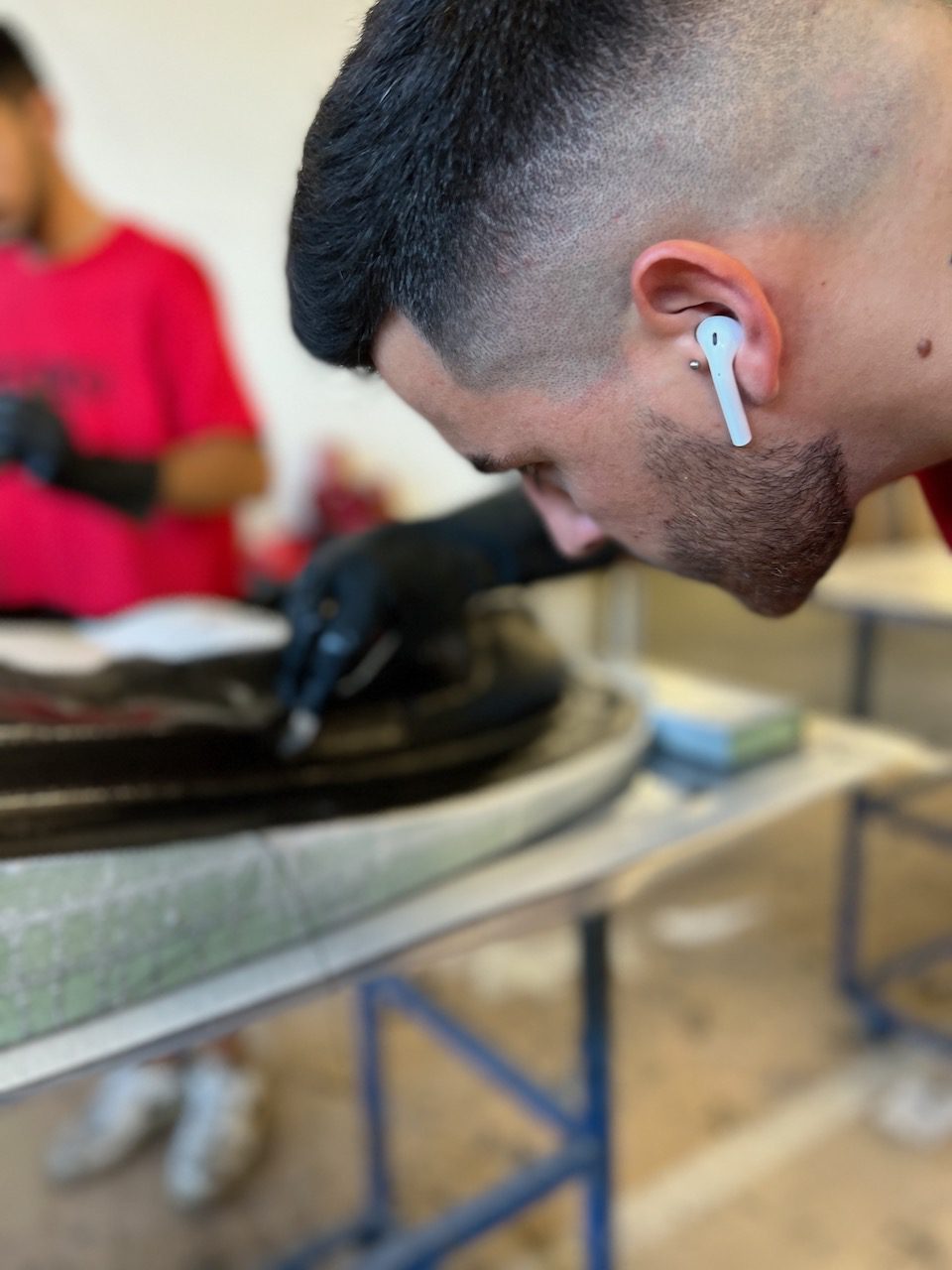
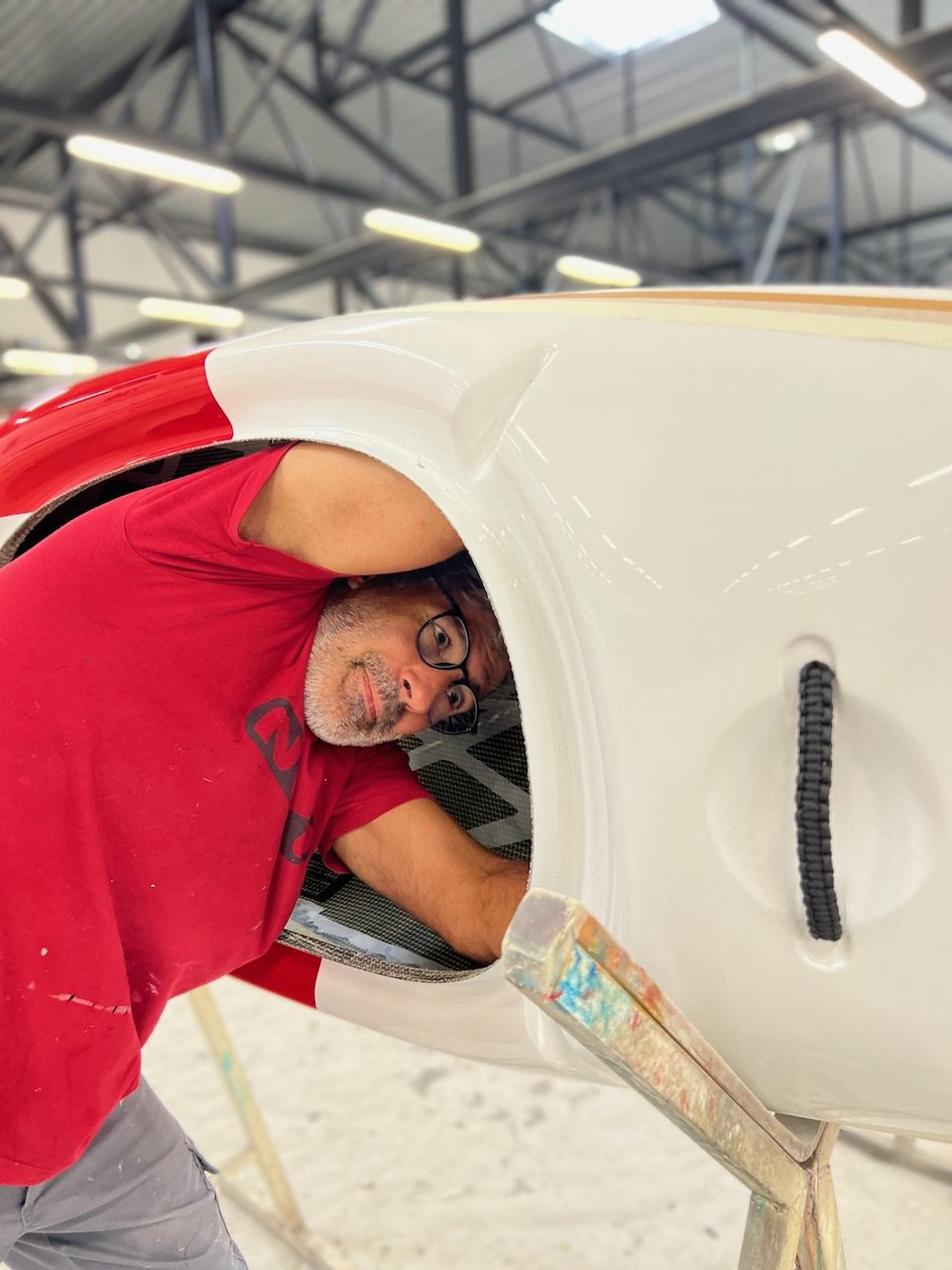
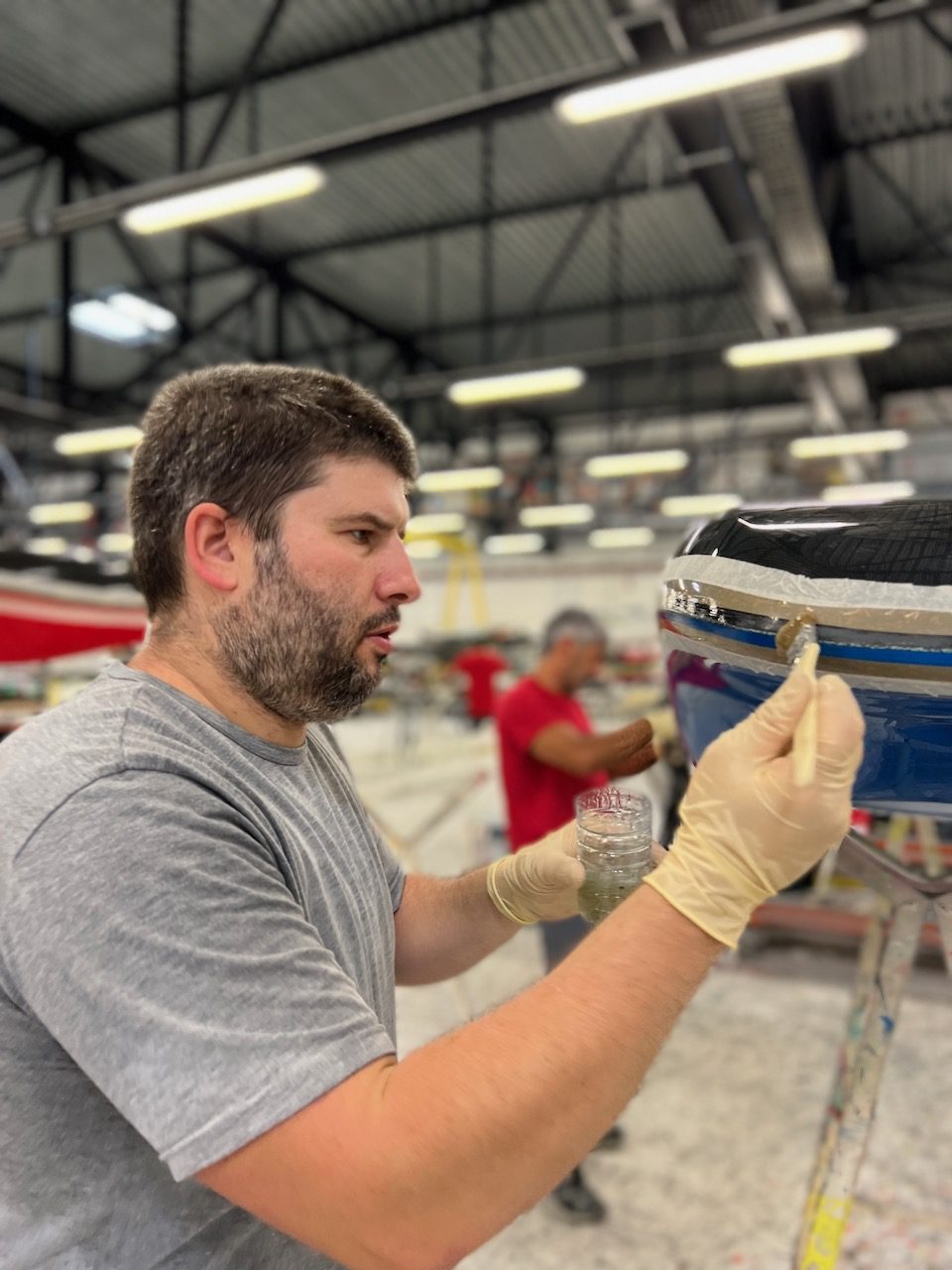
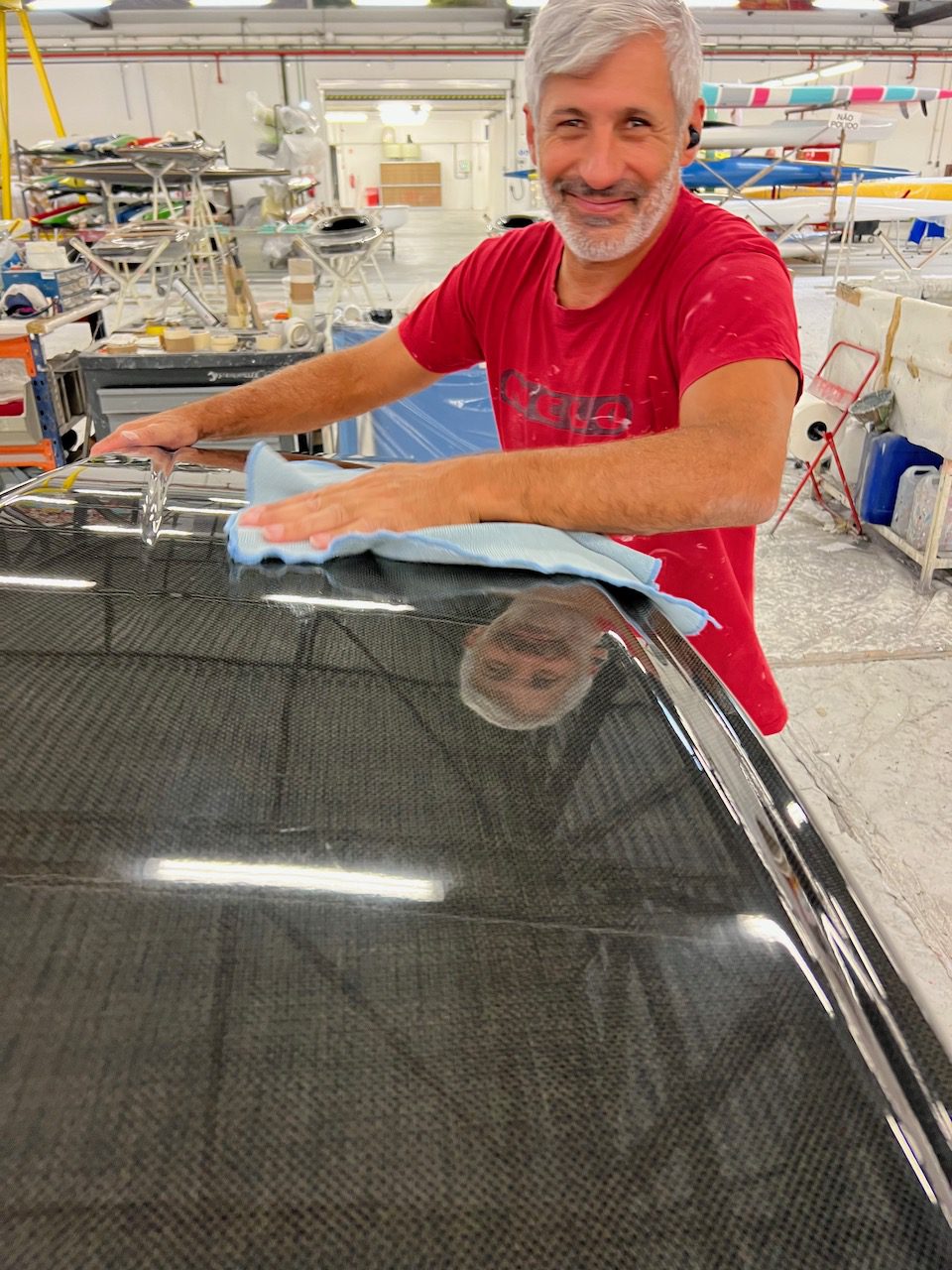
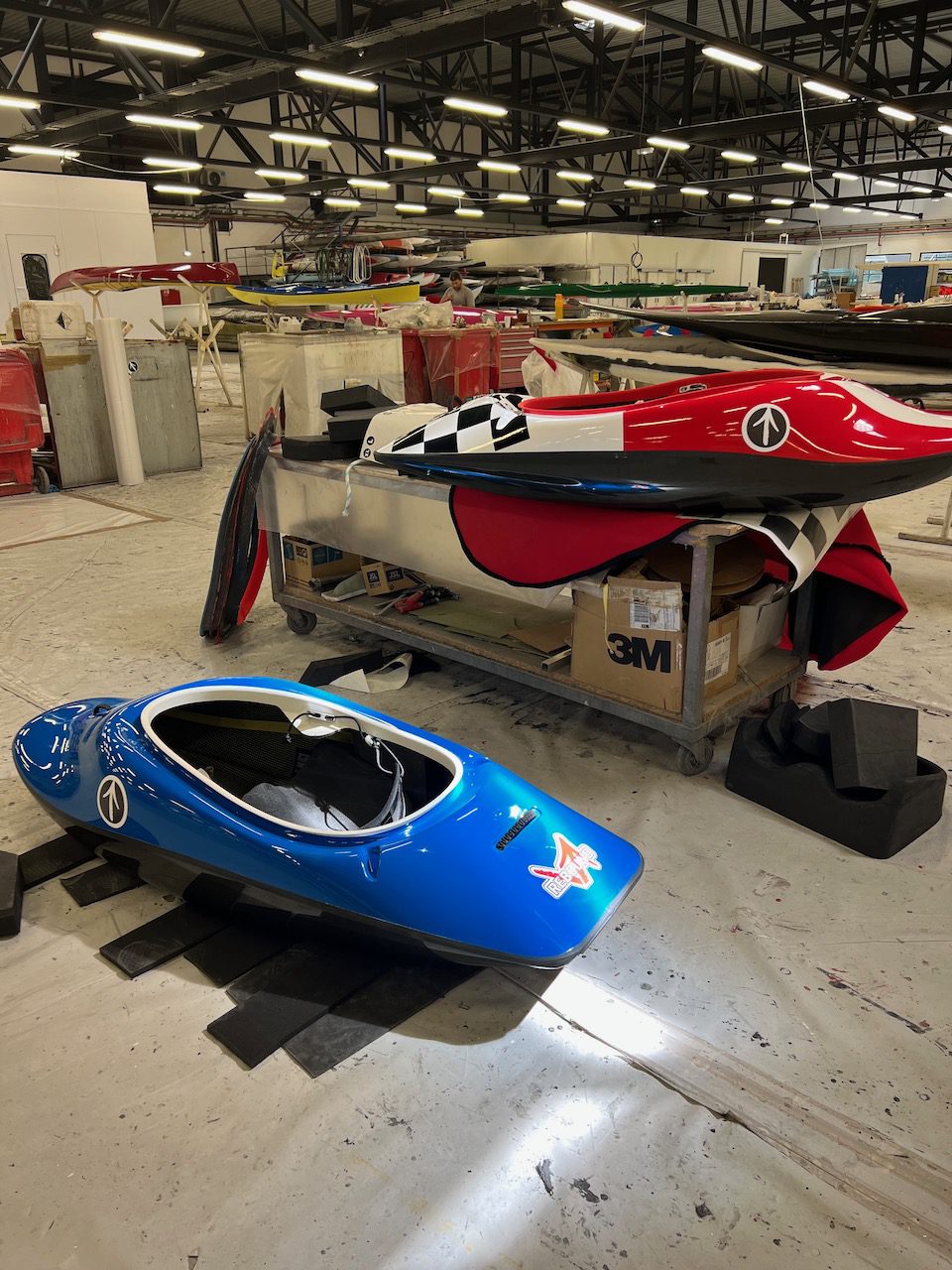

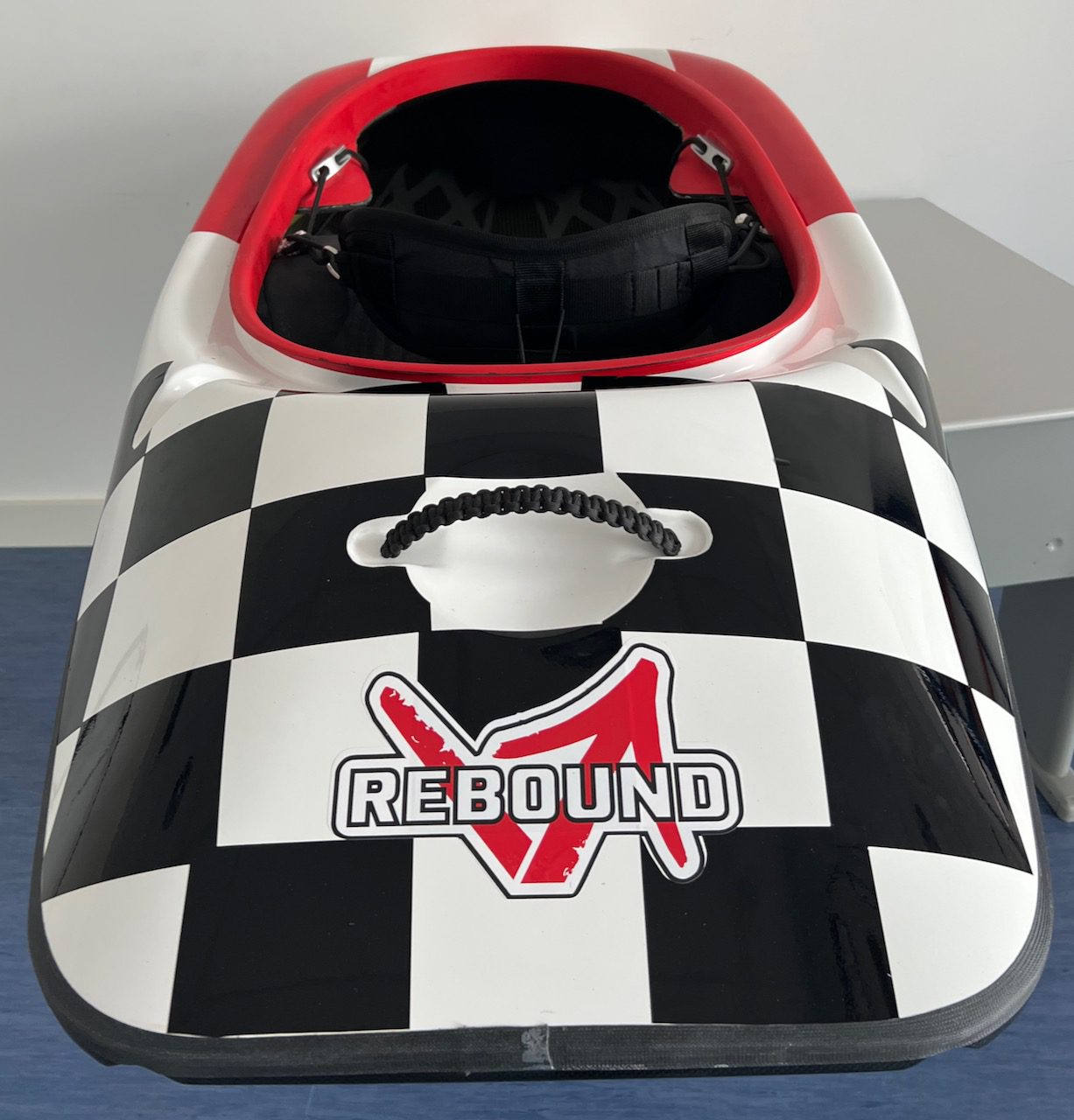
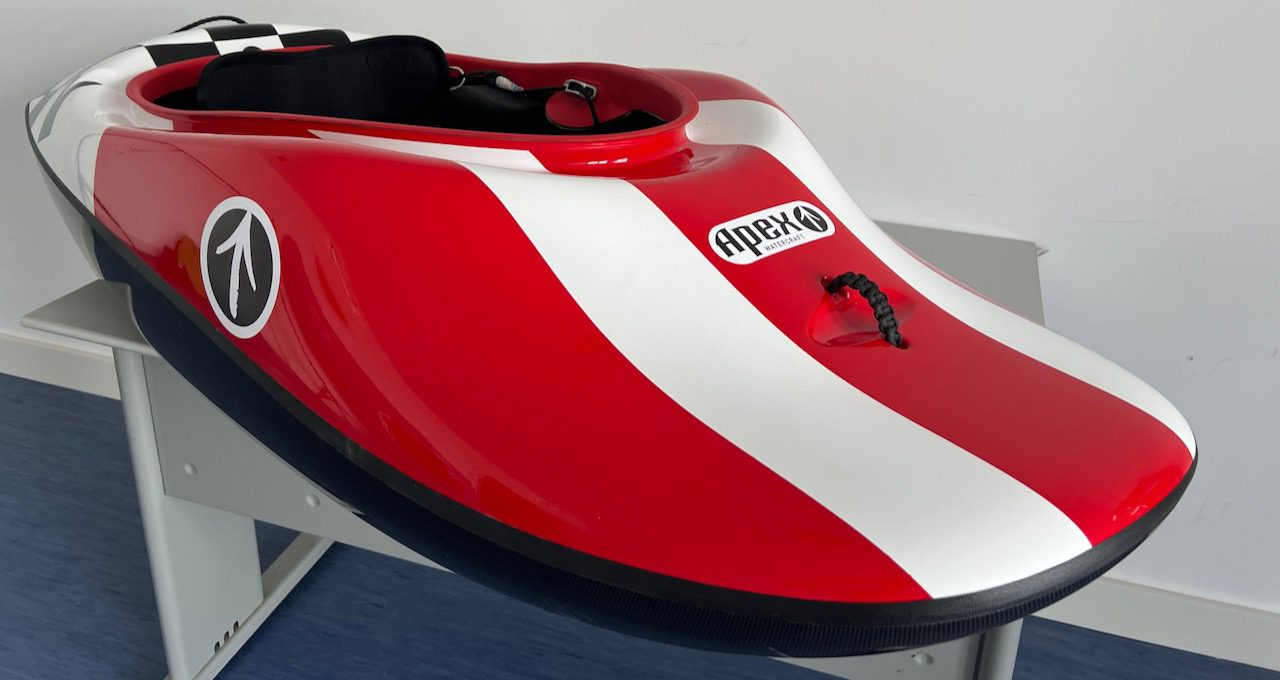

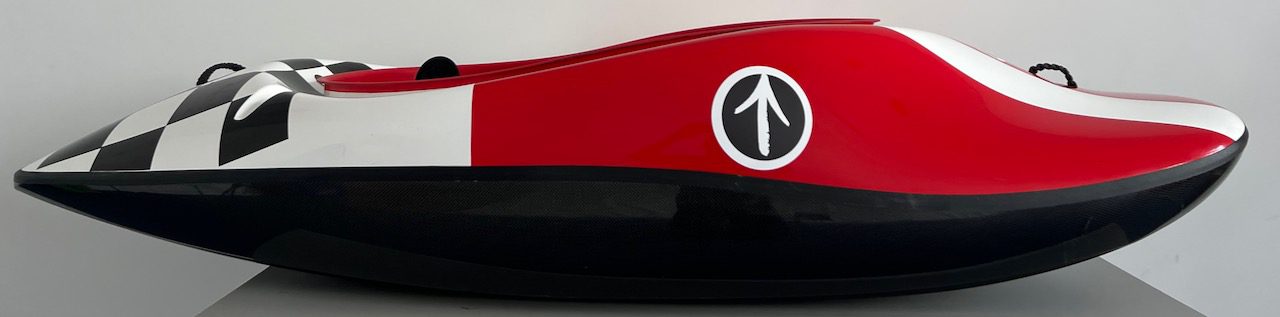

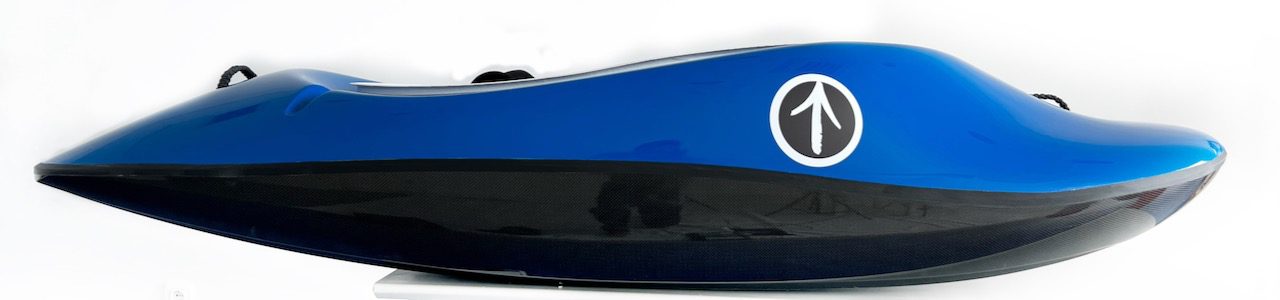
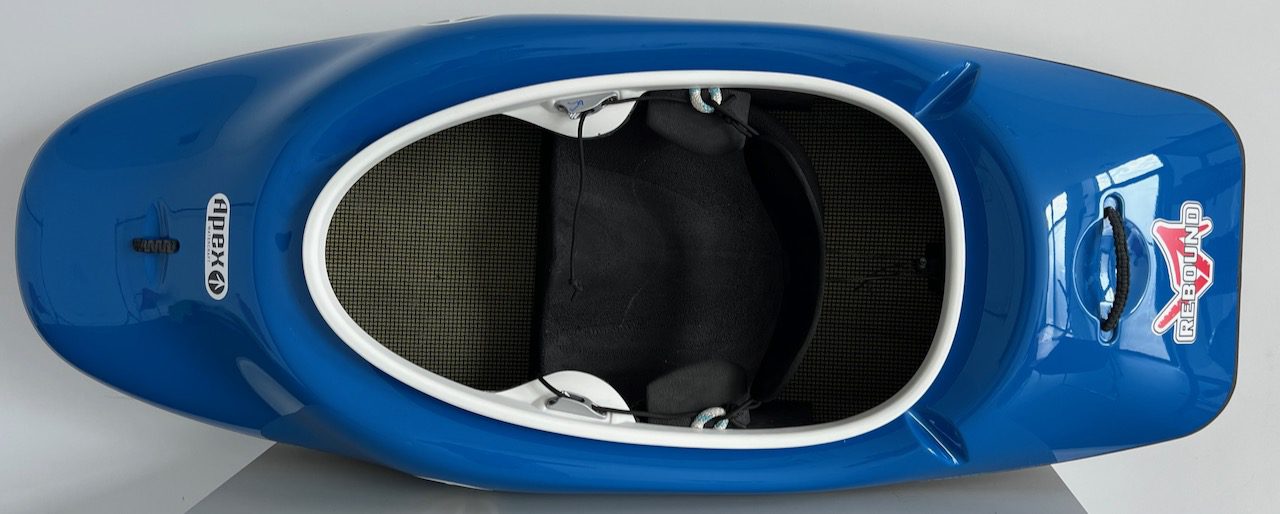
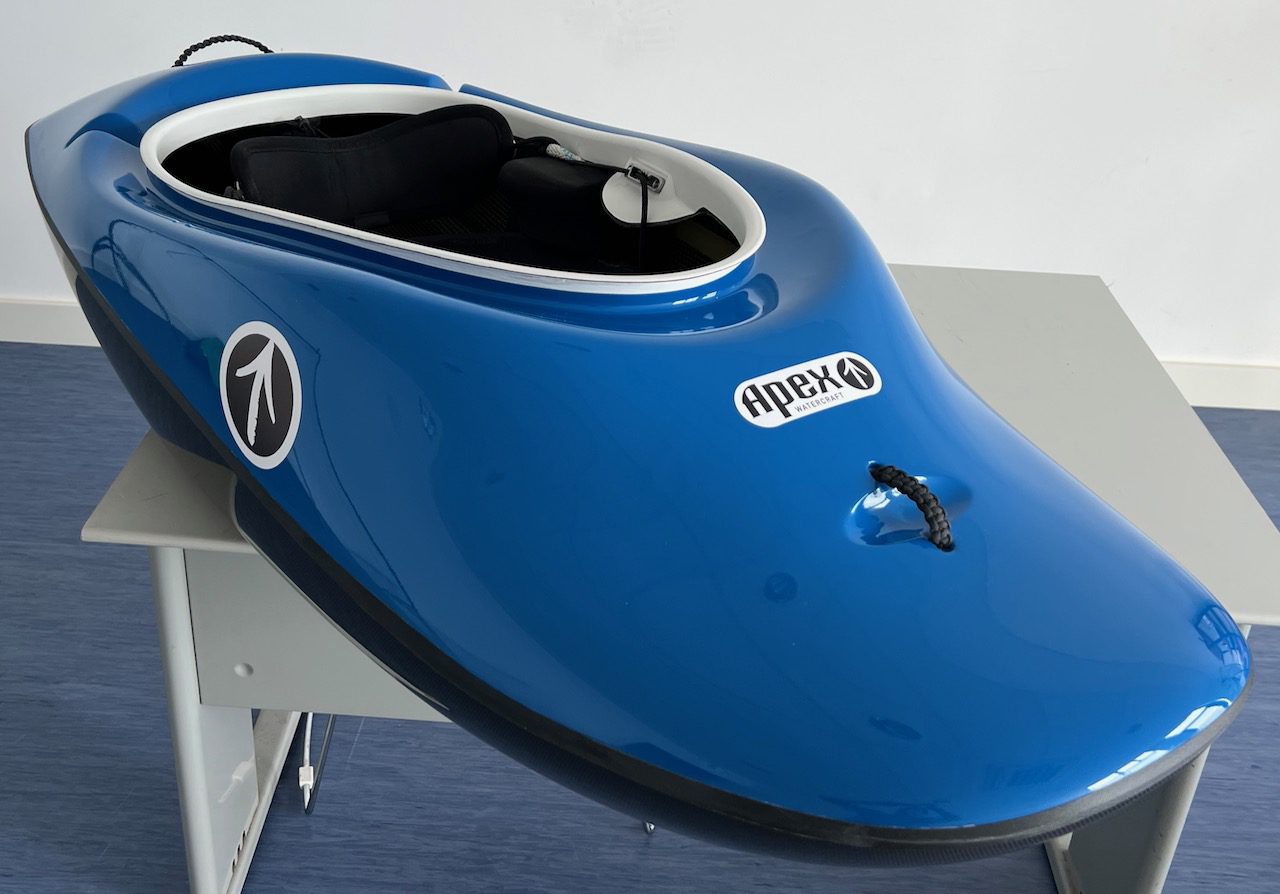

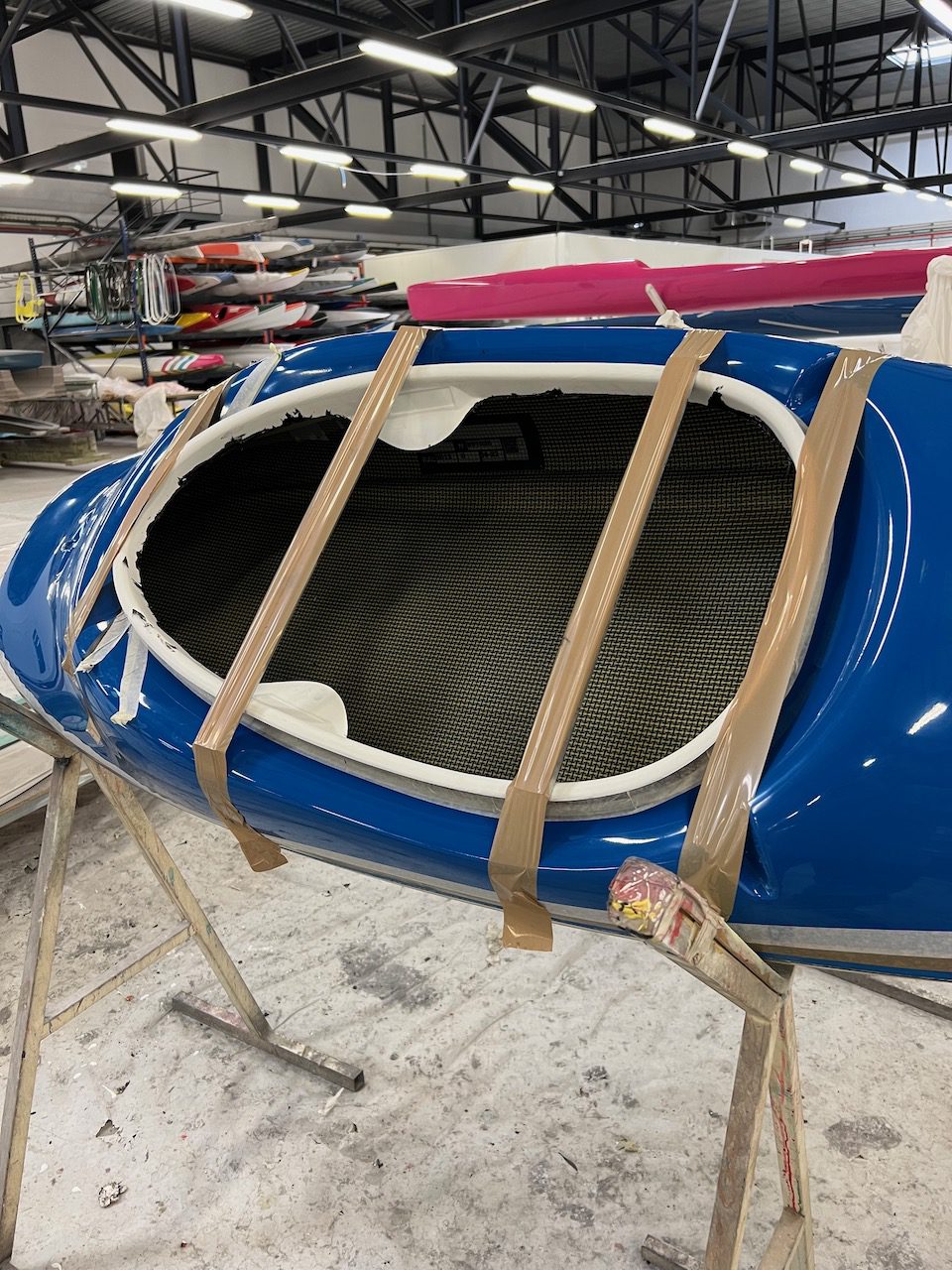
🙂
EJ