Quality isn’t a marketing term. Quality can be measured, seen, felt, and experienced on the water. Here are the steps taken and outcomes that result from those steps to create the undeniable quality when you see, touch, and paddle this boat. Luckily, my dad taught me most of this by the time I was 10 years old with R/C model airplanes, and model boat building. Implementing it and having it be a reality is another thing to knowing how to.
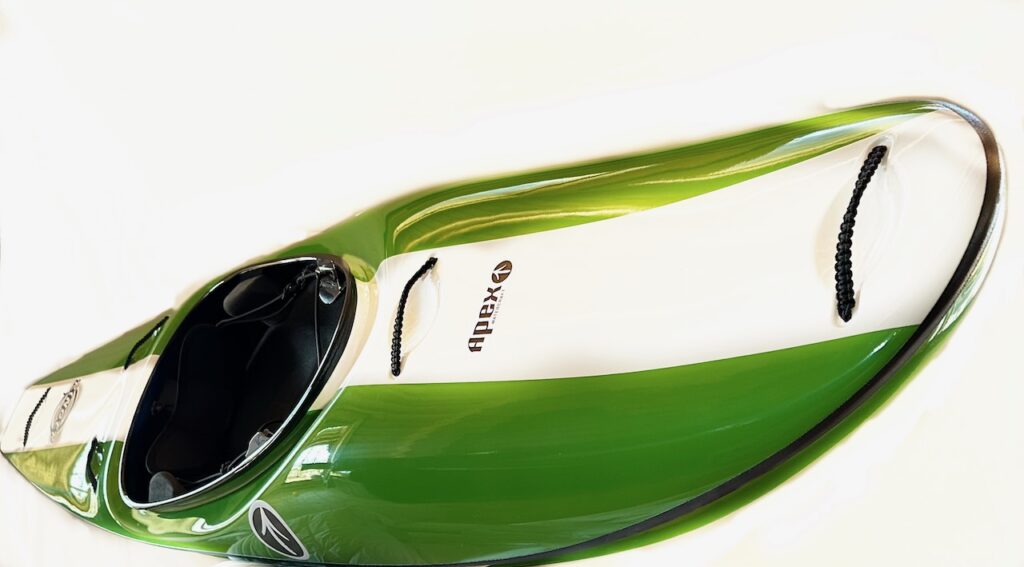
Areas you can control and create a quality product:
Design- This is the most subjective, due to body type, paddling locations, paddling style, goals, etc. however a boat can be the “Fastest of its type” Can be the biggest looping, or easiest to cartwheel, etc.. This post is about the physical quality assuming the design is what you want. (I have plenty of videos and writing about the design).
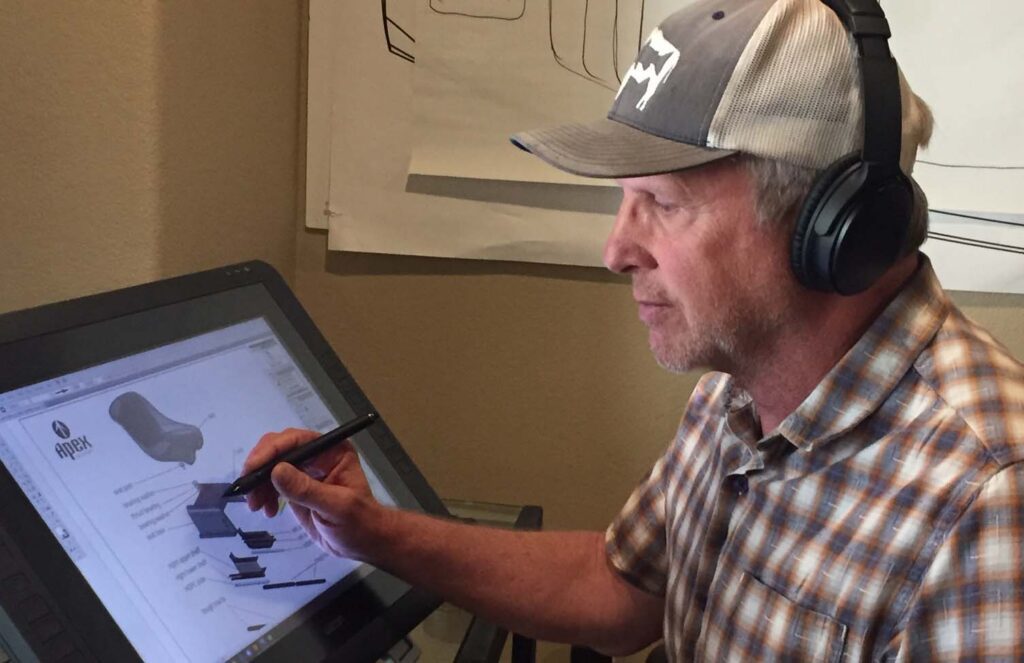
What goes into making a carbon fiber boat that is 17.5 pounds, has seemingly perfect surfaces, seams, and carbon fiber layup?
First thing required is setting the goal of producing a specific quality. Apex is the brand name chosen, and by definition Apex means “The top or highest part.” , so that helps me create my own marching orders and determine when it is “good enough”.
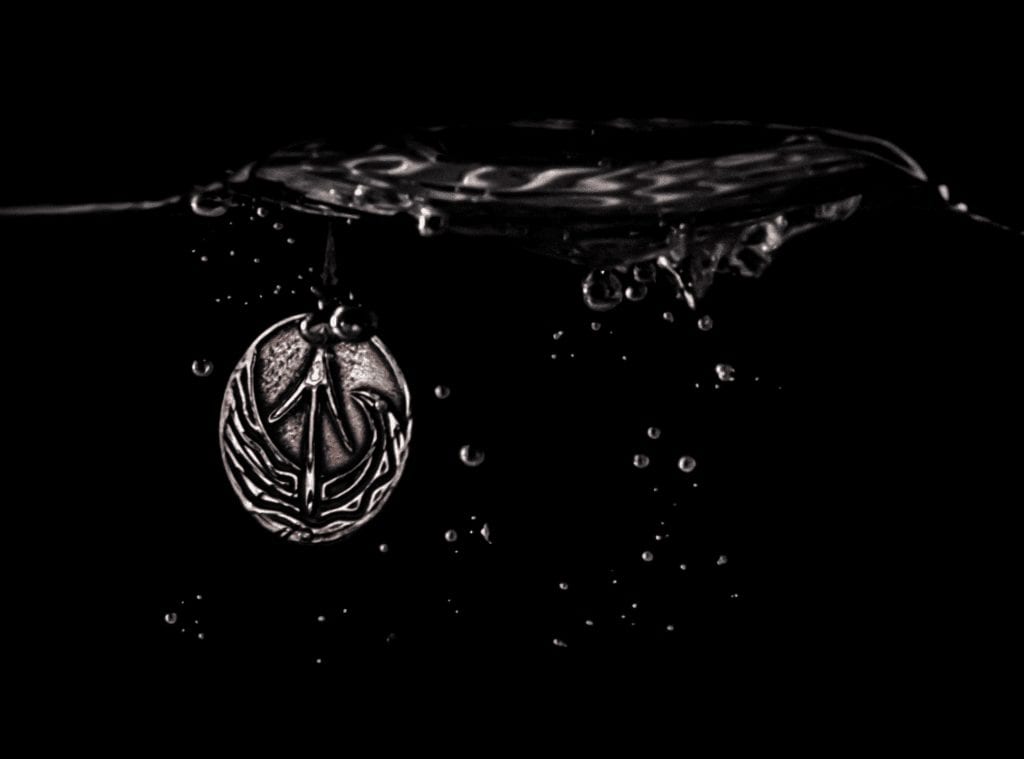
Let’s start with why the boats are so shiny and smooth- how do pull that off?
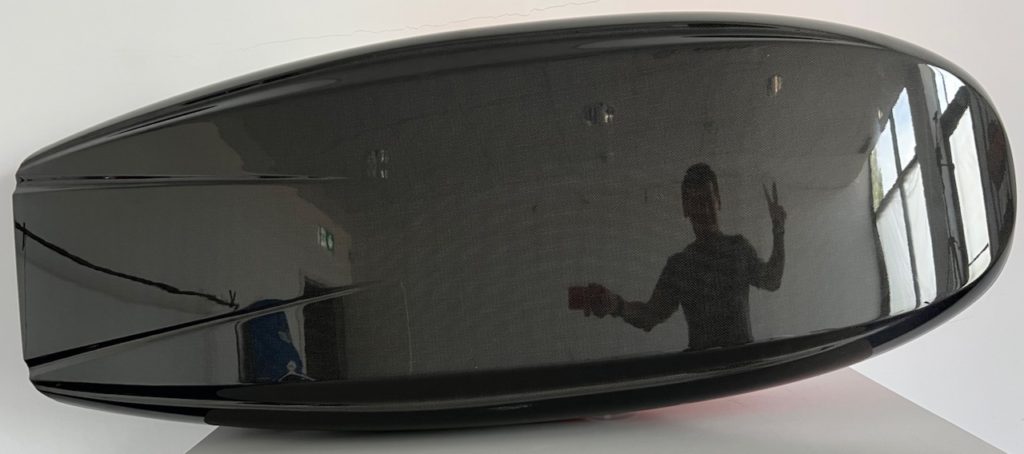
The mold is cut by machine with “perfect surfaces” created by CAD, by Mark Nordstrom. The surfaces were faired and created in a way that if duplicated all of the way to the final boat, they would not have any “WOWs” or waffles, weird spots, etc.. how do you know if your boat is like that? The technique is to look at the surfaces in the light- looking down at an angle on them and seeing if the reflection is smooth like a mirror, or if it bends the light, or in severe cases, simply has waves, and poorly managed shapes.
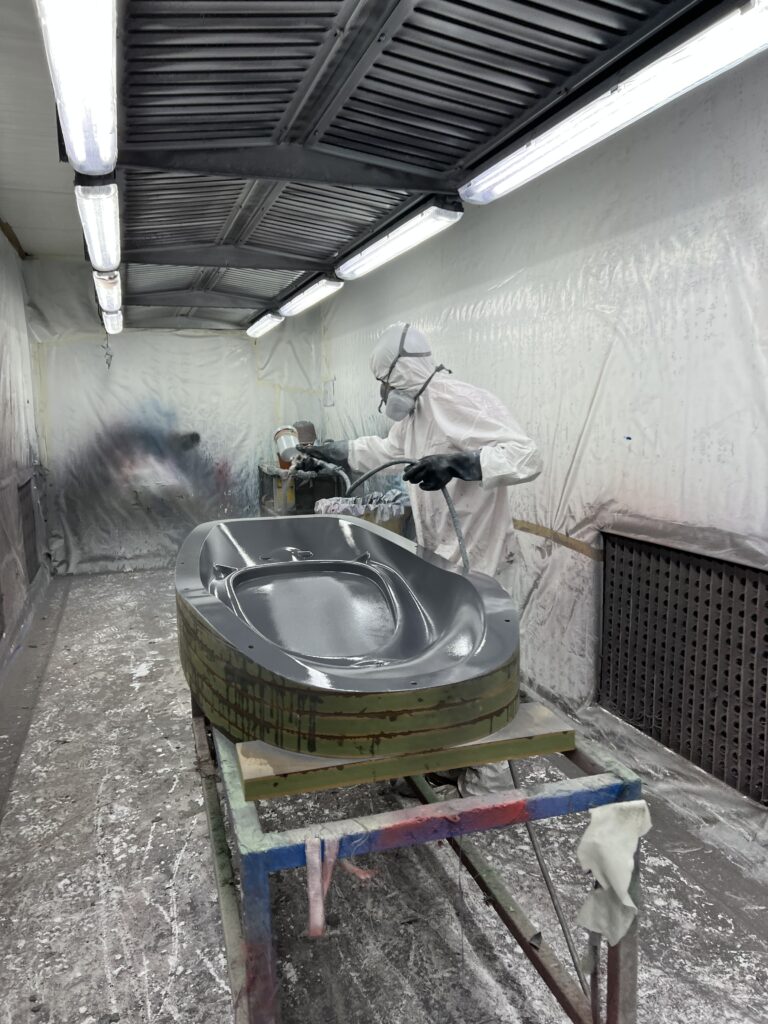
How we managed to create near perfect shapes on the Rebound and Ringer-
1. Mold was cut by machine with the CAD surfaces properly faired.
2. Plug was made out of that mold and faired with care and wet sanded and polished until it was a mirror without distortion in the reflection.
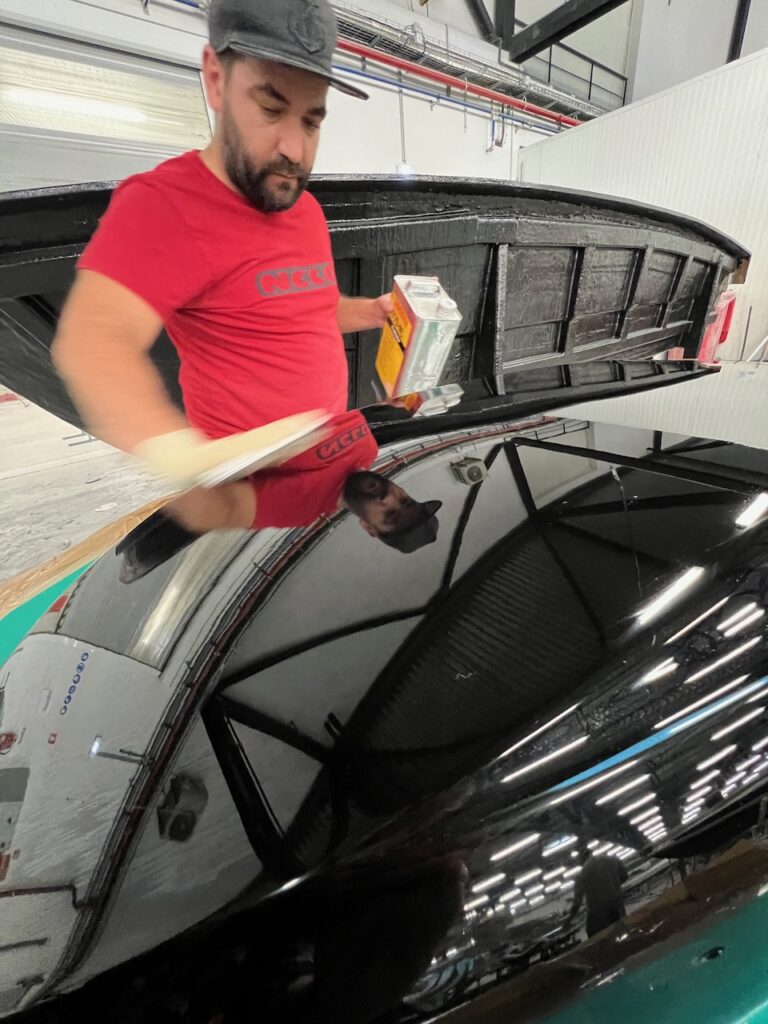
3. Mold was pulled off of that “near perfect” (Nothing is perfect that is done by hand) plug, and also faired, polished, framed to hold its shape.
4. Boats are laid up and pulled out of a near-perfect mold. Every time a boat is pulled out, the mold goes to a mold expert, who cleans the mold, checks for scratches or other imperfections and corrects if needed, or applies a release to it and stages it up for the next boat. Mold release is a step that can also turn a beautiful finish into a muddled one. Release build-up, etc. are culprits if not done properly.
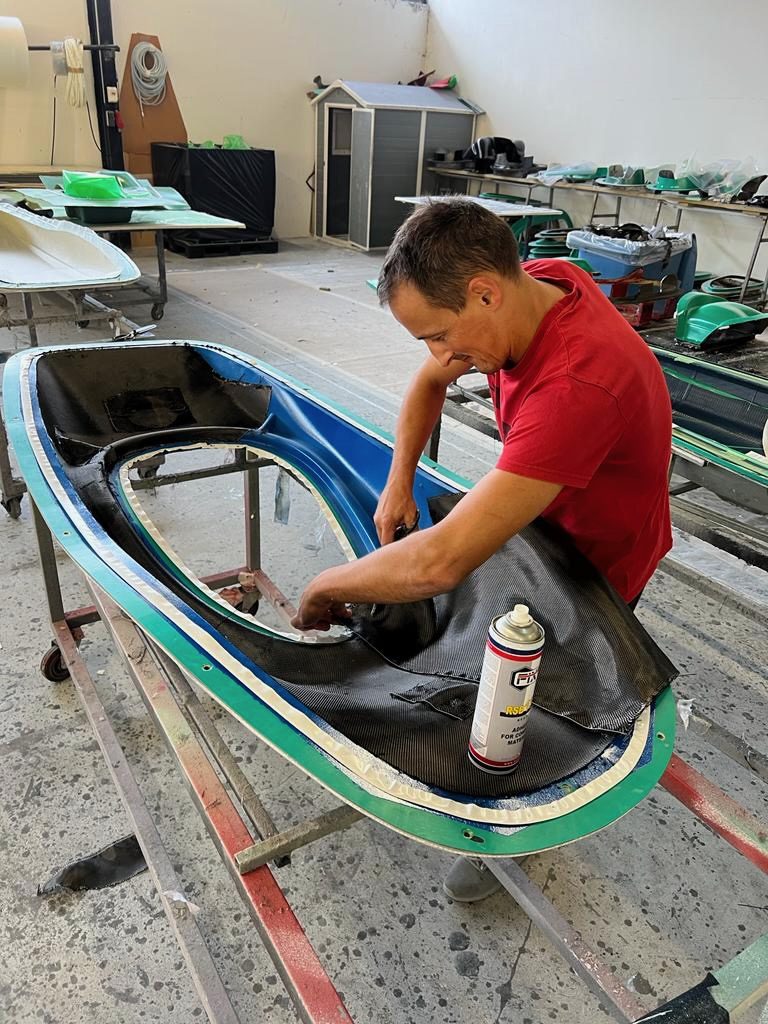
5. Our boats are molded as a “one piece” so the trimming is only the “flashing” on the parting line, which is where the resin flows out of the deck and hull and squeezes between the two molds. It is trimmed off and done by hand. Another opportunity for human error or great craftsmanship. Only the best people with a steady/confident hand are put on that process, as well as trimming out the cockpit area. You have a similar process with plastic boats as well and the difference between somebody really good and just “somebody” is night and day. One “nick” or over grinding, or undergrinding and you have a visible defect on your boat. I have yet to see one mistake on any of my parting lines or cockpit rims. The team I have working on my boats at Nelo are the best in each department. Watching them in action is inspiring to anyone who enjoys seeing amazing artisans at work.
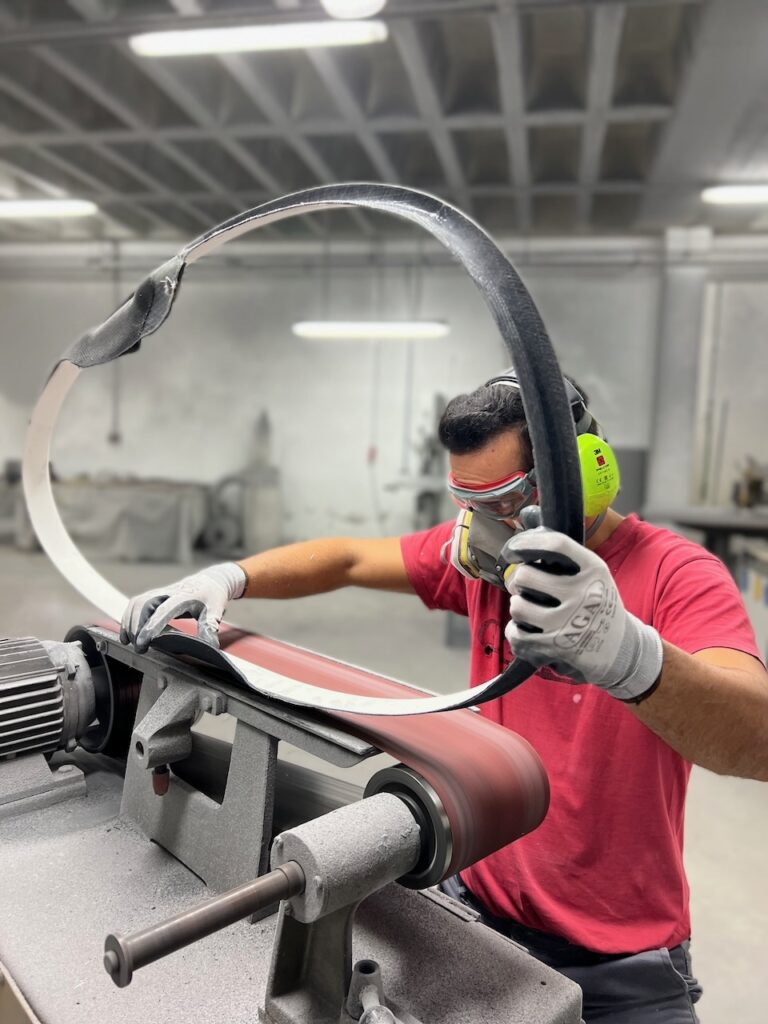
6. Assembly- cockpit rim, outside seam, and Grab handles are first and each one also requires a lot of expertise to do and have the work be aesthetically pleasing. cockpit rim is installed inside the cockpit opening (Apex)- Other brands have a different process. By installing in the opening if the rim is properly trimmed and well designed, it can be carbon fiber laminated in smoothly with no rough edges and be bomber strong. If you feel the rim by rubbing your hands around the outside trimmed edge, or inside trimmed and laminated edge it will be smooth to the touch, fair, and look like a machined edge. Craftsmanship- period. Not a machined edge, it was done by a human, on a grinder/ and touched up with gel coat, and inspected to meet my criteria. I don’t set unreasonable goals, knowing how hard manufacturing is, and how duplicating over and over again is difficult. However, the bar is set at the top, and the team can duplicate that level simply due to their own expertise, equipment, training, and enough time allocated for them to succeed.
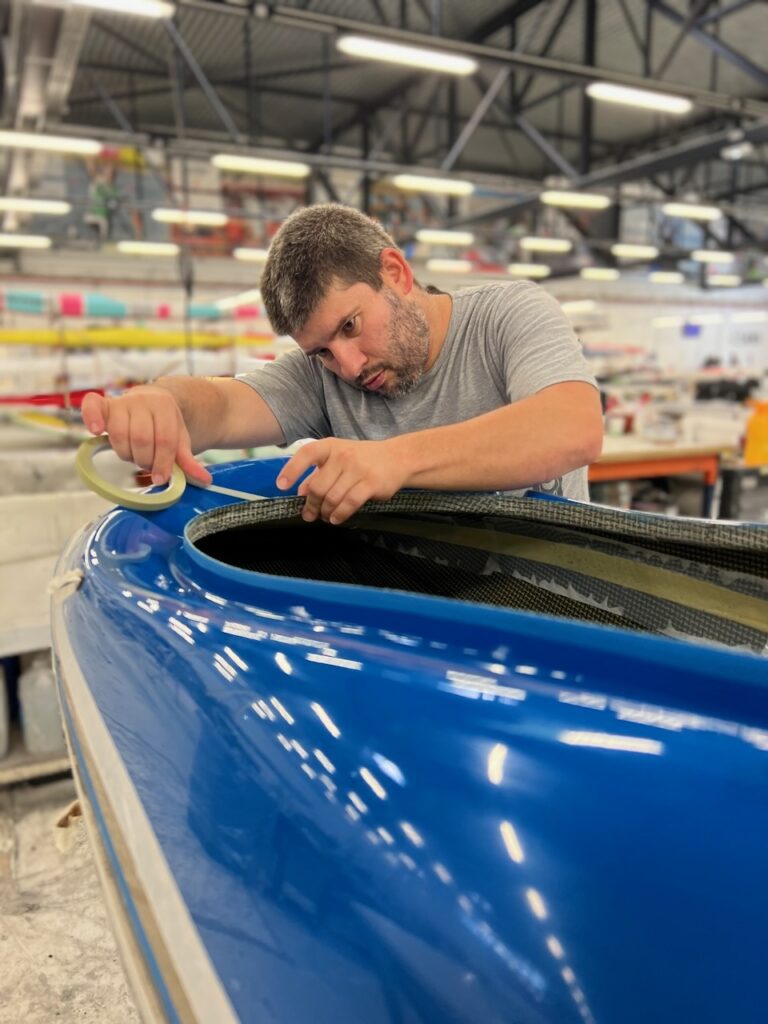
7. Small parts- Seat Hip Pads, Backband, footblock, etc. Here I took a slightly different approach. The seat is 100% mini-cell foam. It is CNC machined, one at a time- each one taking about 2 hours on the machine. same with the hip pads. The benefit is a lightweight seat and pads that offer extreme levels of support. Oversized seat that eliminates the need for a “happy Seat”. An invention of mine from 2005 that is still in use today. The long, elevated seat provides support of your hamstring allowing you to “Push down” on it when you drop an edge and adds comfort/control. The seat is raw foam. Grey, no cool cloth glued onto it with graphics. This was purely function. Adding cloth adds weight. It also prevents you from being able to shave foam off to customize it if you want. At JK I invented the Sweet Cheeks, which is an almost instant form-fitting seat to add to your plastic seat to turn a large women’s butt plastic seat into a custom seat. It is an awesome piece of equipment, but it weighs 1 pound or more when wet. My new foam seat provides more support for less weight. Aesthetically it isn’t a “finished piece” like the hull. however, performance is key here. I can make a beautiful shiny hull that is super lightweight for on water performance. The seat to be high performance, as of today, is done the way I am doing it and it is made out of foam.
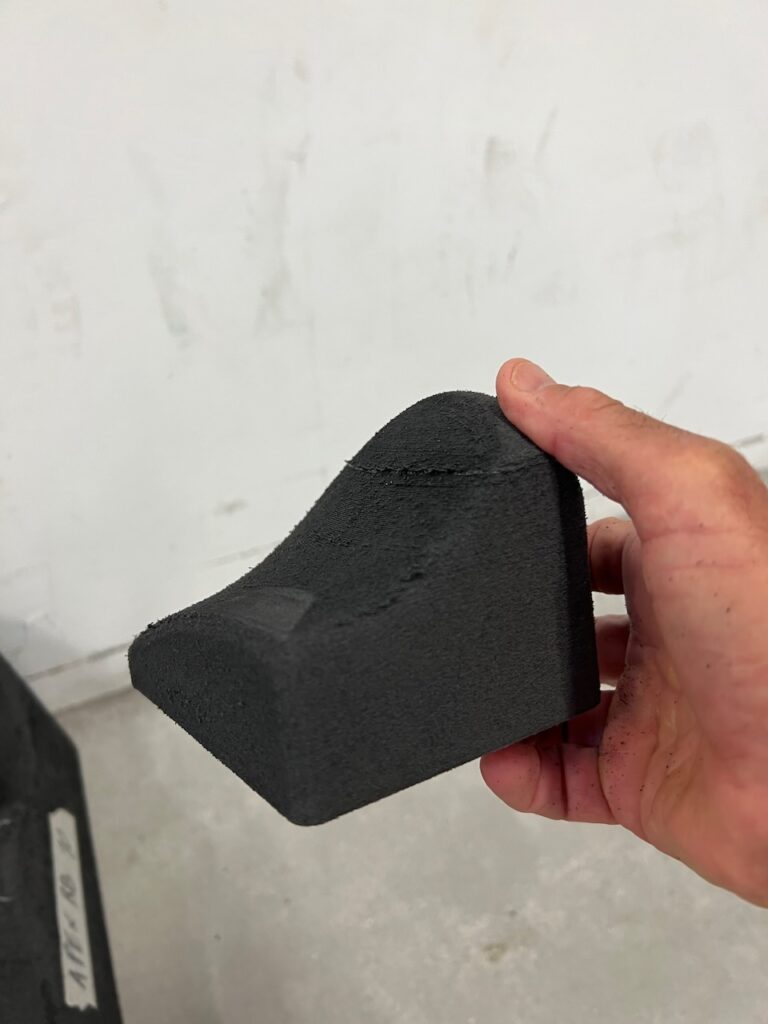

7. Weight- 17.5 pounds for Rebound, 23 pounds for Ringer (both mediums)- that is all in ready to paddle, with everything included. (what my boat weighs if right now) The hull of the Rebound is only 13.5 pounds. 4 pounds is outfitting: which include cockpit rim (.7 pounds), grab handles, walls, seat, backband, ropes, footblock, hip pads, etc..
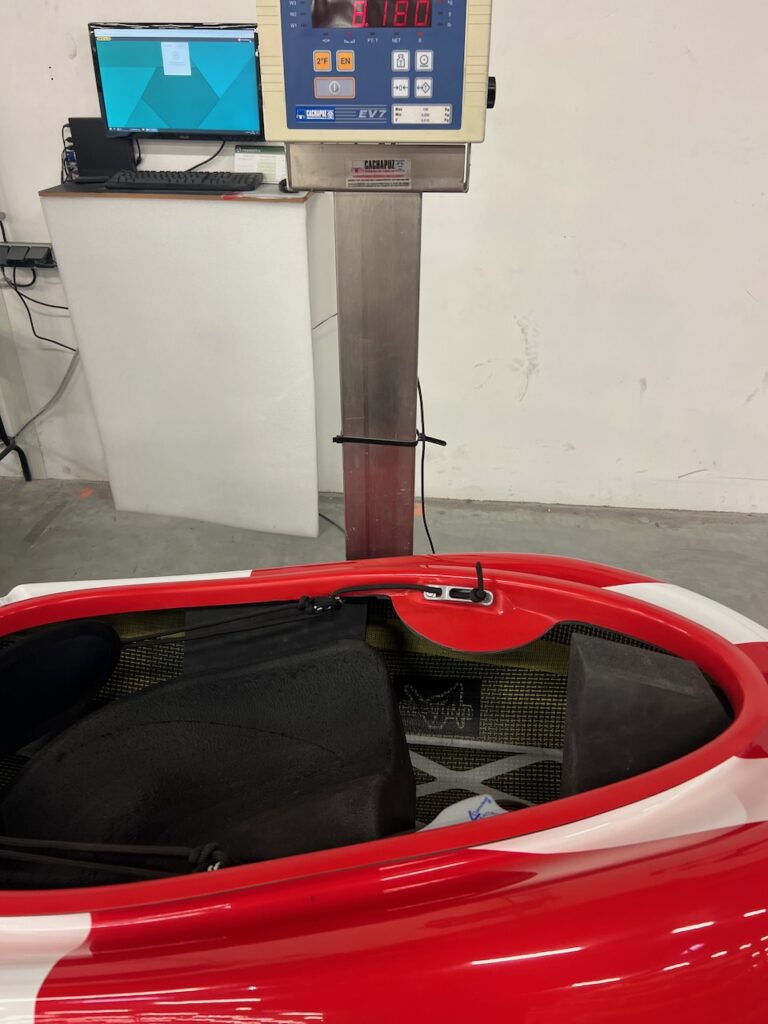
Another “secret” to making the boat super lightweight and stiff. Wet Lay-up. Infusion process requires either a soric type material or perforated foam. Both increase the weight quite a bit. Molders prefer infusion as it is clean, less smell, and efficient, but it is not the way to get the lightest boat that is also stiff. The extra weight savings takes more work. The Tyr fishing kayak combines an infusion deck that has a secondary wet layup process afterwards to add the foam that saves 7 pounds over doing a 100% infusion process in that larger boat. The way you can use Infusion, and not have it be heavy is to not use a “core” material, such as Soric, or Foam. There are places that it makes sense to do that on the deck, mostly.
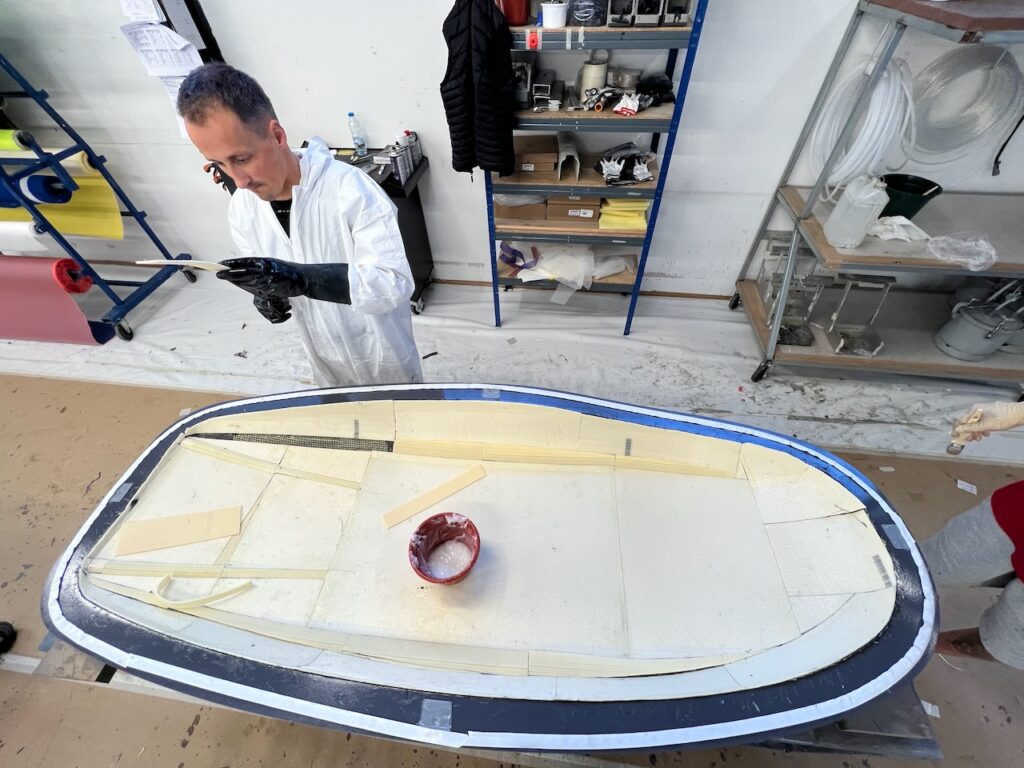
I was just going to put up another photo of another color boat we just made but lots of people seemed curious about how they are made. If there was a single ingredient that could be copied, it would be tempting to keep it to myself. But when the ingredients that make the difference are a combo of facilities, materials, taking your time to get the design, plugs, and molds right (cockpit rim changes added 45 days to the time in the end), and the actual boat building process. Even the final step of wet sanding and buffing each boat out. That step isn’t “normal”. Boats come out of a great mold shiny. However, imperfections, dull spots, etc. are possible, and will happen. They are also possible to turn into near perfection with time and expertise (both cost money, of course)
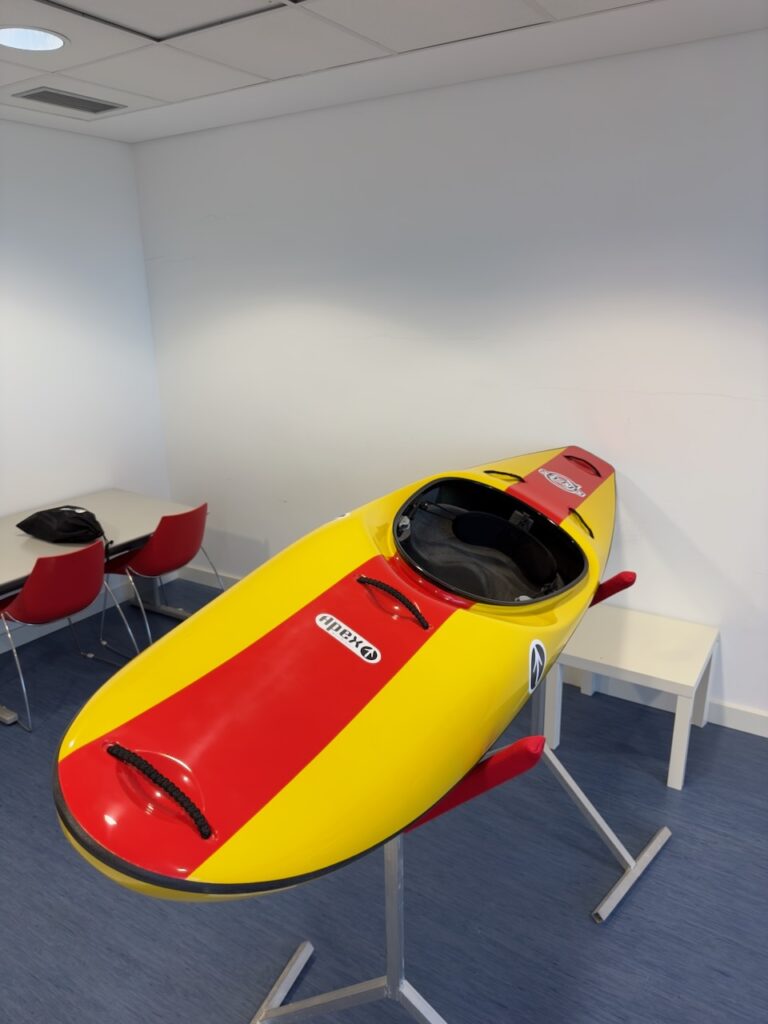
An Apex boat is far from perfect- FYI. Improvements, more innovation, etc. are part of the plan. I am far from perfect and make mistakes, don’t maximize everything that could be maximized. My goal is to put in the extra work and time and money if needed to get as good as I can and as long as that is the “Apex” of what is available, it is a success. From there, I can try to outpace the competition and hopefully create a situation where friendly competition drives progress for everyone.
Fun stuff. Lots of hard work, not much money in it, but fun and rewarding. Especially since I get to use my own wares for my personal enjoyment daily. I am lucky to have a manufacturing partner in Nelo, who is putting their best people on the job. 40 years of composite kayak making, focusing on Sprint Racing kayaks and winning about 75% of the medals in world championships and Olympic events in that sport and the clear first choice among the best athletes. Why? Because of consistent quality. Working with people that are happy to race you after work, because they are athletes as well is also super cool.
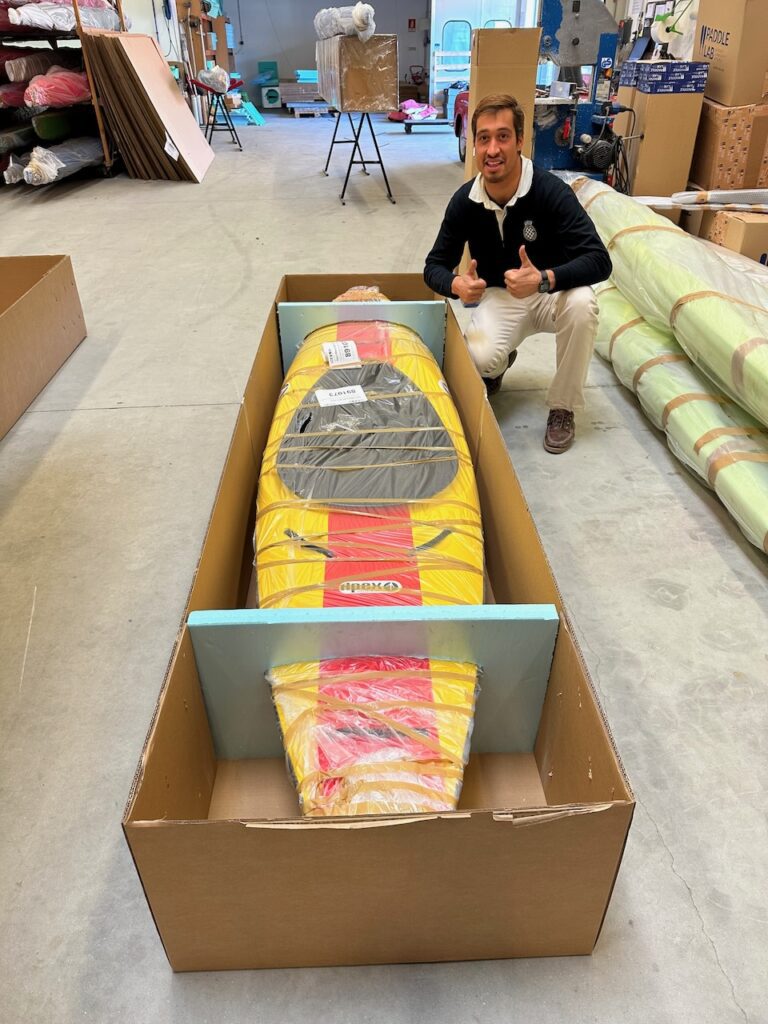
Meanwhile- I just got off the water. I just did my first “World Championships Training Session”. Up until now I was training for USA Team Trials. Now that I made the team, it is “Worlds Training” time.
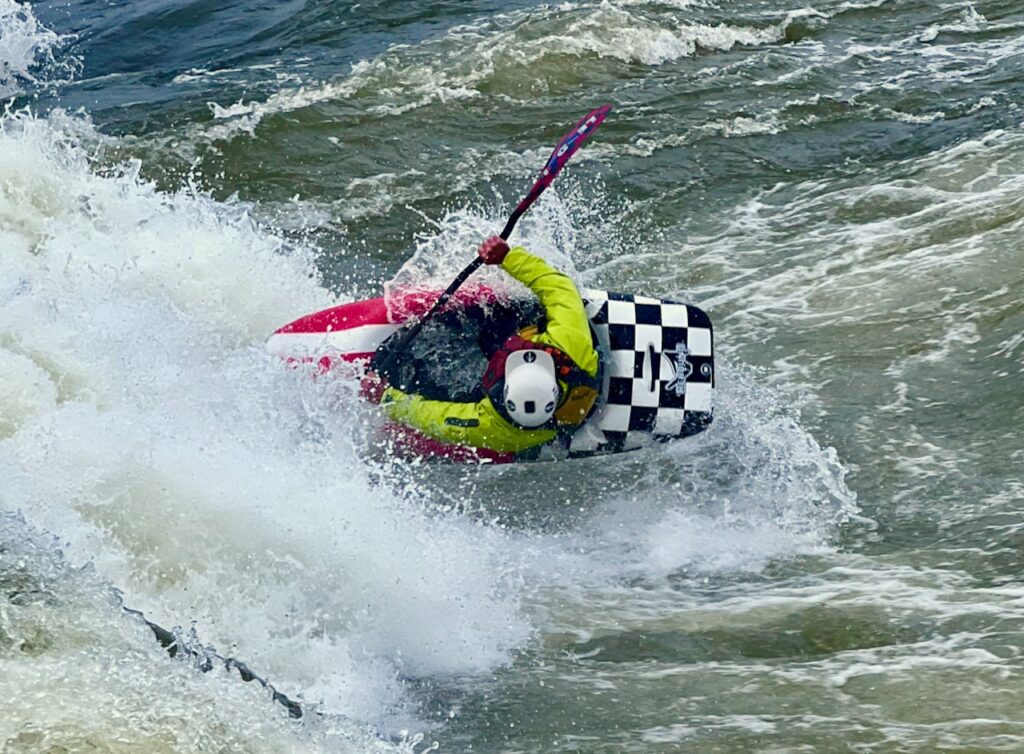
See you on the river!
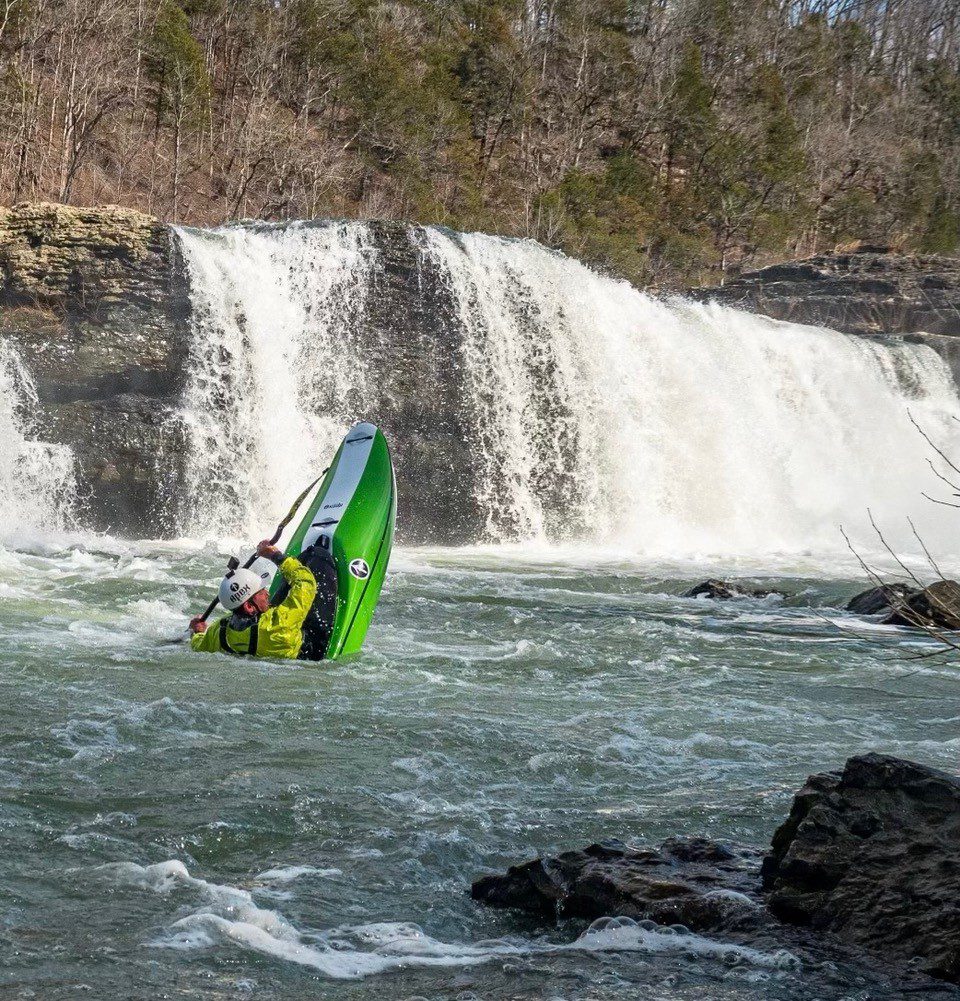
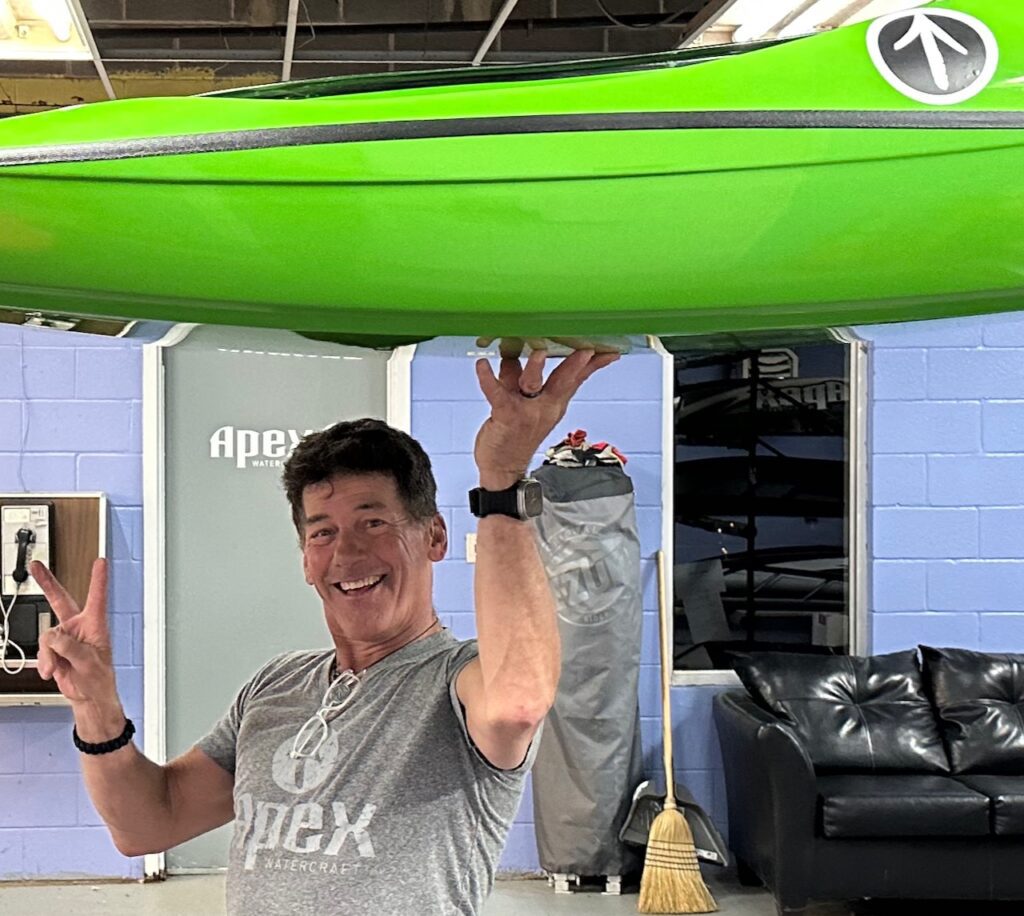

EJ